5 Common Pitfalls to Avoid When Procuring Industrial Cable Assemblie...
Industrial cable assemblies are the lifelines of manufacturing, automation, and energy systems, transmitting power and data critical to operations. However, selecting the wrong cables can lead to costly downtime, safety hazards, and compliance issues.
- Overlooking Environmental Requirements
Pitfall: Choosing cables based solely on electrical specs without considering the operating environment.
Consequences: Premature failure due to temperature extremes, moisture, chemicals, or abrasion.
Solutions:
Match materials to conditions:
Silicone or TPE jackets for high heat (>100°C) or flexibility.
PUR (polyurethane) for oil and chemical resistance.
Stainless steel braiding for abrasive environments.
Verify IP ratings:
IP67/IP68 for submersion in washdown areas.
IP69K for high-pressure steam cleaning (food/pharma).
Case Example: A packaging plant used standard PVC cables in a humid environment, leading to insulation breakdown. Switching to PUR-jacketed IP67 cables reduced replacements by 70%.
2. Ignoring Compliance and Certification Gaps
Pitfall: Assuming all cables meet industry standards without verifying certifications.
Consequences: Fines, failed audits, or incompatibility with machinery.
Critical Standards to Check:
UL/CSA Certification: Mandatory for North American markets.
IEC 60332 for flame resistance in hazardous areas.
RoHS/REACH for hazardous substance restrictions (EU).
3-A Sanitary Standards for food-grade applications.
Red Flag: Suppliers unable to provide test reports or compliance documentation.
3. Sacrificing Quality for Cost Savings
Pitfall: Prioritizing low-cost options without evaluating lifecycle costs.
Consequences: Frequent failures, increased downtime, and higher TCO (Total Cost of Ownership).
Cost vs. Quality Balance:
Cheap connectors: Prone to corrosion, leading to signal loss.
Under-spec’d shielding: EMI/RFI interference in automated systems.
Thin insulation: Susceptible to cuts in high-vibration zones.
Rule of Thumb: Invest in ISO 9001-certified suppliers with proven track records, even if initial costs are higher.
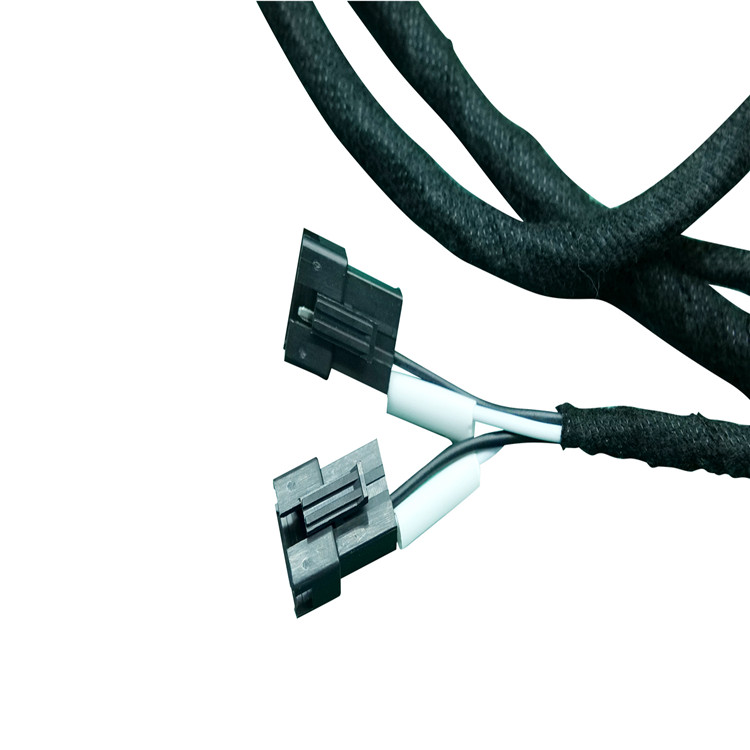
4. Neglecting Customization Needs
Pitfall: Opting for off-the-shelf assemblies when unique requirements exist.
Consequences: Poor fit, performance issues, or installation delays.
When to Customize:
Length and bend radius: Avoid tension or kinking in tight spaces.
Connector types: Match M12/M8 codes (A, B, D, X) to sensor/PLC compatibility.
Shielding: Add braided + foil layers for high EMI environments.
Color coding: Simplify maintenance in complex systems.
Case Example: A robotics integrator saved 20% in labor costs by using pre-terminated cables with angled connectors, eliminating field modifications.
5. Failing to Plan for Scalability
Pitfall: Procuring cables only for current needs without future-proofing.
Consequences: Expensive retrofits when upgrading machinery or expanding facilities.
Scalability Strategies:
Bandwidth headroom: Choose Cat6a over Cat5e for future Ethernet upgrades.
Modular connectors: Use M12 sockets compatible with multiple device types.
Supplier partnerships: Work with vendors offering volume discounts and rapid prototyping.
Trend Alert: Demand for Single-Pair Ethernet (SPE) and fiber-optic hybrid cables is rising with IIoT adoption.
Bonus: How to Vet Suppliers Effectively
Audit Facilities: Ensure they have in-house testing (e.g., TDR, VNA).
Request Samples: Test cables in real-world conditions before bulk orders.
Check Lead Times: Avoid suppliers with inconsistent stock or long turnaround.
Review Warranties: Opt for vendors offering ≥3-year warranties.
Case Study: Automotive Assembly Line Failure
A car manufacturer sourced non-compliant cables for its welding robots, resulting in:
EMI-induced misfires due to unshielded cables.
Melted jackets near high-temperature weld zones.
Fix: Switched to shielded, high-temperature cables with UL and IEC certifications. Downtime dropped by 45%, and ROI was achieved in 8 months.