Cable Assembly Applications in Petrochemical Industry
- Core Challenges for Cable Assemblies in Petrochemical Environments
Petrochemical facilities (e.g., refineries, chemical plants, offshore platforms) demand cables that withstand:
Explosion Hazards: Flammable gases (e.g., methane, ethylene) require ATEX/IECEx-certified components.
Chemical Corrosion: Exposure to acids, alkalis, solvents, and hydrocarbons.
Extreme Temperatures: High heat (exceeding 150°C near reactors) and subzero conditions (arctic or deep-sea applications).
Mechanical Stress: Vibration, impact, and repeated flexing (e.g., pump stations, compressor lines).
2. High-Reliability Cable Assembly Selection Guidelines
2.1 Explosion-Proof Design and Certification Compliance
Explosion Protection Types:
Flameproof (Ex d): Suitable for Zone 1/2 areas (e.g., storage tanks, reactor peripherals).
Intrinsic Safety (Ex i): For Zone 0 hazardous areas (e.g., gas leak-prone zones).
International Standards:
ATEX 2014/34/EU: EU explosion protection directive.
IEC 60079: Global explosion protection standards.
GB 3836: China’s national certification (NEPSI).
2.2 Corrosion-Resistant Materials and Structural Design
Jacket Materials:
Fluoropolymers (FEP/PFA): Resistant to strong acids, alkalis, and solvents (ideal for acid wash units).
Polyurethane (PUR): Oil-resistant and durable for pump/valve areas.
Shielding and Insulation:
Double Shielding (braided copper + aluminum foil): Mitigates EMI from VFDs and high-power motors.
Cross-Linked Polyethylene (XLPE) Insulation: High-temperature resistance and dielectric strength.
2.3 Mechanical and Environmental Durability
Flexibility Optimization:
High-Flex Conductors: Multi-stranded fine copper wires for 100,000+ bend cycles (e.g., robotic arms).
Kevlar Reinforcement: Enhances tensile strength for offshore platform installations.
Protection Ratings:
IP68/IP69K: Waterproof and dustproof for high-pressure washdowns.
UV-Resistant Jackets: For outdoor pipelines and exposed installations.
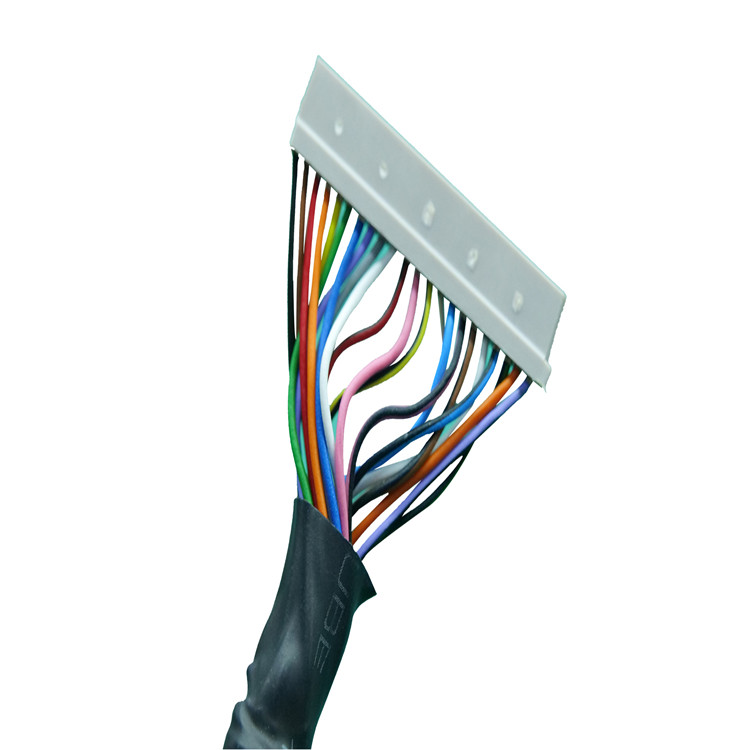
- Typical Applications and Tailored Solutions
3.1 Refinery Reactor Zones
Challenges: High temperatures, hydrogen exposure, vibration.
Solutions:
Silicone-Jacketed Cables: Withstand 200°C + ATEX Ex d certification.
Stainless Steel Armor: Mechanical protection and EMI shielding.
3.2 Chemical Processing Units
Challenges: Sulfuric acid, chlor-alkali leaks.
Solutions:
FEP Jackets + Tinned Copper Shielding: Corrosion and oxidation resistance.
Molded Sealed Connectors: Prevent chemical ingress.
3.3 Offshore Oil Platforms
Challenges: Salt spray, dynamic loads, low temperatures.
Solutions:
EPDM Rubber Jackets: Resistant to salt corrosion and temperatures down to -40°C.
Anti-Torsion Design: For dynamic cable routing on floating platforms. - Compliance Testing and Maintenance Best Practices
Testing Standards:
IEC 60502: Power cable testing protocols.
IEEE 1202: Flame resistance (vertical flame test).
Preventive Maintenance:
Infrared Thermography: Detect overheating at joints.
Insulation Resistance Testing: Use megohmmeters to monitor insulation health. - Future Trends: Smart and Sustainable Solutions
Smart Cable Systems:
Fiber Optic Sensing: Real-time monitoring of temperature, strain, and partial discharges.
Self-Diagnostic Connectors: IoT-enabled health reporting to SCADA systems.
Eco-Friendly Materials:
Halogen-Free Jackets: Compliance with RoHS/REACH regulations.
Recyclable Designs: Reduce carbon footprint in petrochemical operations.