A Comprehensive Guide to Selecting Cable Assemblies for Industrial Au...
Introduction
In industrial automation, cable assemblies serve as the lifelines of machinery, robotics, and control systems. Their performance directly impacts operational efficiency, safety, and uptime. However, selecting the right cable assemblies for harsh factory environments—with challenges like continuous motion, extreme temperatures, EMI interference, and chemical exposure—requires a strategic approach. This guide explores critical factors, materials, and standards to optimize cable assembly selection for industrial automation applications.
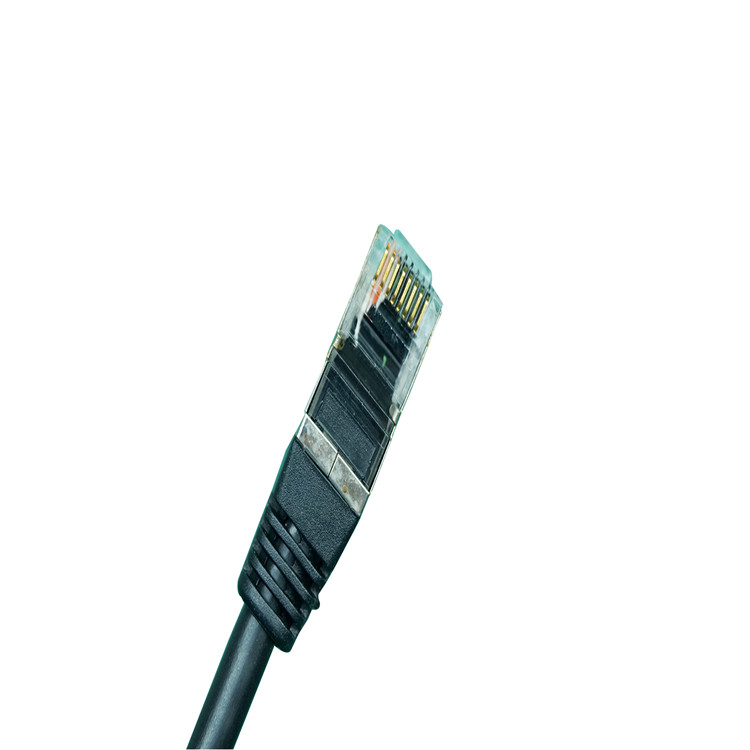
Key Challenges in Industrial Automation Environments
Mechanical Stress: Frequent flexing, torsion, and vibration in robotic arms or conveyor systems.
Environmental Hazards: Exposure to oils, coolants, UV radiation, and temperature extremes (-40°C to 150°C).
Electrical Interference: EMI/RFI noise from motors, drives, and high-voltage equipment.
Space Constraints: Compact cable routing in densely packed machinery.
Critical Selection Criteria for Cable Assemblies
1. Flexibility and Durability
High-Flex Cables:
Designed for robotic arms or cable carriers with >1 million flex cycles.
Use fine-stranded conductors and thermoplastic elastomers (TPE) or PUR jackets.
Torsion-Resistant Cables:
Helical shielding and layered constructions for rotating applications (e.g., CNC spindles).
Abrasion Resistance:
Reinforced jackets (e.g., PVC with nylon overbraid) for drag chains or rough surfaces.
2. Environmental Resistance
Temperature Ratings:
Silicone or fluoropolymer (FEP, PTFE) insulation for high-temperature zones (e.g., near furnaces).
Cold-resistant materials like TPU for freezer logistics.
Chemical Resistance:
PUR jackets for oil and coolant resistance; PTFE for aggressive solvents.
IP Ratings:
IP67/IP68 seals for washdown areas (e.g., food processing) or dusty environments.
3. Electrical Performance
Shielding:
Foil + braided shielding (85% coverage) to block EMI in drive systems or servo motors.
Double-layer shielding for sensitive signal cables (e.g., EtherCAT, Profibus).
Voltage and Current Ratings:
Match conductor size and insulation thickness to power demands (e.g., 24V control vs. 480V motor cables).
Signal Integrity:
Twisted pairs or coaxial designs for high-speed data (Ethernet, USB 3.0).
4. Compliance and Certifications
Industry Standards:
UL 758 for appliance wiring, IEC 61076 for connectors, and ISO 13849 for safety-rated systems.
Specialized Certifications:
FDA-compliant jackets for food and pharma; ATEX/IECEx for explosive atmospheres.
Material Selection Guide
Application Recommended Materials
High-Flex Robotics PUR jacket, TPE insulation, tinned copper shielding
High-Temperature Zones Silicone rubber, PTFE, or fiberglass braiding
Washdown Areas Stainless steel connectors, PUR/IP68-rated cables
EMI-Sensitive Systems Double-shielded cables with ferrite cores
Case Studies: Matching Cables to Applications
Automotive Assembly Line
Challenge: Robotic welders require cables resistant to sparks, oils, and continuous flexing.
Solution: High-flex PUR cables with aramid yarn reinforcement and EMI shielding.
Pharmaceutical Packaging
Challenge: Frequent sterilization with hydrogen peroxide vapor.
Solution: PTFE-insulated cables with sealed connectors (IP69K).
Warehouse AGVs (Automated Guided Vehicles)
Challenge: Cables must withstand torsion during sharp turns and battery acid exposure.
Solution: Torsion-rated cables with oil-resistant TPE jackets and spiral shielding.
Common Pitfalls to Avoid
Overlooking Bend Radius: Exceeding minimum bend radii accelerates jacket cracking.
Mismatched Shielding: Using foil-only shielding in high-EMI environments leads to signal loss.
Ignoring Maintenance: Lack of strain relief or proper routing causes premature failure.
Future Trends in Industrial Automation Cables
Smart Cables: Integrated sensors for real-time monitoring of temperature, wear, or EMI.
Lightweight Designs: Carbon fiber or composite materials for mobile robotics.
Sustainable Materials: Recyclable jackets and halogen-free flame retardants.
Modular Connectors: Tool-less connectors for rapid maintenance in Industry 4.0 systems.