Choosing Industrial Cable Components for High-Temperature Environment...
1. Challenges in High-Temperature Environments
Cables in high-heat settings face unique risks:
Insulation Degradation:
Polymers soften, crack, or melt, leading to short circuits.
Conductor Oxidation:
Metal conductors (e.g., copper) oxidize, increasing resistance and energy loss.
Mechanical Weakness:
Heat reduces flexibility, causing brittleness and susceptibility to vibration damage.
Fire Hazards:
Flammable insulation materials can ignite under extreme heat.
2. Key Criteria for High-Temperature Cable Components
When selecting cables for high-heat applications, prioritize these factors:
Temperature Rating:
Match the cable’s maximum operating temperature (e.g., 90°C, 150°C, 250°C+) to the environment.
Thermal Stability:
Materials should resist thermal expansion, oxidation, and chemical breakdown.
Flame Resistance:
Use fire-retardant or fire-resistant cables to comply with safety standards.
Mechanical Durability:
Resistance to abrasion, oil, chemicals, and UV radiation.
3. Optimal Materials for High-Temperature Cables
Insulation Materials
Silicone Rubber:
Temperature Range: -60°C to +200°C (short-term up to 250°C).
Advantages: Flexible, UV-resistant, and flame-retardant. Ideal for ovens, furnaces, and heavy machinery.
Cross-Linked Polyethylene (XLPE):
Temperature Range: Up to 150°C.
Advantages: High dielectric strength, chemical resistance. Common in power distribution and motor windings.
Polytetrafluoroethylene (PTFE):
Temperature Range: -200°C to +260°C.
Advantages: Exceptional heat and chemical resistance. Used in aerospace, petrochemicals, and high-precision industries.
Mineral Insulated (MI) Cables:
Temperature Range: Up to 1,000°C (with magnesium oxide insulation and copper sheath).
Advantages: Fireproof, waterproof, and corrosion-resistant. Ideal for critical safety systems and nuclear plants.
Conductor Materials
Copper:
Standard choice for conductivity but prone to oxidation at high temperatures. Opt for tinned copper to resist corrosion.
Nickel-Plated Copper:
Enhanced oxidation resistance for temperatures exceeding 200°C.
Stainless Steel:
Used in MI cables for extreme heat and mechanical stress.
Jacketing Materials
Fluoropolymers (e.g., FEP, PFA):
Withstand up to 200°C and resist chemicals, oils, and moisture.
Fiberglass:
Used as an outer braid in MI cables for fire protection.
4. Application-Specific Solutions
Steel and Foundry Industries
Cables for Ladle Cranes and Furnaces:
Use PTFE-insulated cables with stainless steel armor to handle molten metal splashes and temperatures above 500°C.
Chemical and Petrochemical Plants
Reactor and Pipeline Monitoring:
Silicone-jacketed cables resist acids, alkalis, and hydrocarbons at 150–200°C.
Automotive Manufacturing
Paint Shop and Welding Robots:
High-flex silicone cables endure continuous movement and heat from welding arcs (up to 250°C).
Energy and Power Generation
Gas Turbines and Boilers:
MI cables ensure uninterrupted power and signal transmission in 800–1,000°C exhaust systems.
5. Standards and Certifications
Ensure compliance with industry standards:
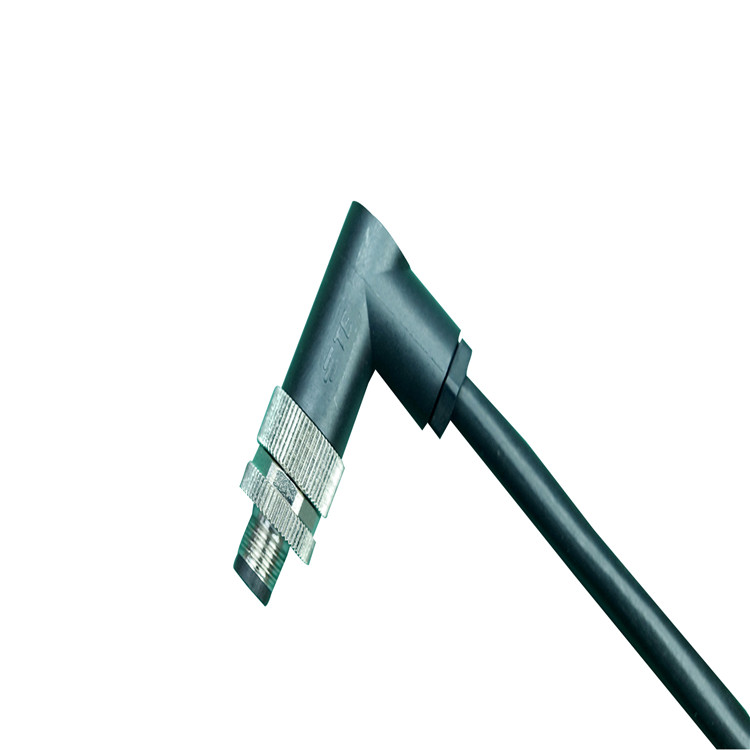
UL 44/UL 83: Certifies thermoplastic-insulated wires for up to 90°C.
IEC 60502: Specifies XLPE cables for medium-voltage applications (up to 150°C).
MIL-DTL-22734: Governs PTFE-insulated cables for aerospace and military use.
BS 6387: Tests fire resistance under temperatures up to 950°C.
6. Installation and Maintenance Tips
Avoid Direct Heat Sources:
Route cables away from hot surfaces or use reflective heat shields.
Proper Ventilation:
Prevent heat buildup in cable trays or conduits.
Regular Thermal Imaging:
Detect hotspots or insulation degradation early.
7. Future Trends in High-Temperature Cables
Nanocomposite Insulation:
Materials like silica-nanoparticle-enhanced polymers improve thermal stability.
Self-Monitoring Cables:
Embedded sensors detect temperature spikes and insulation faults in real time.
Eco-Friendly Fire Retardants:
Halogen-free, low-smoke materials reduce environmental impact.