Corrosion Prevention Strategies for Marine and Offshore Engineering C...
In marine and offshore environments, cable assemblies face relentless challenges from saltwater, humidity, temperature fluctuations, and chemical exposure. Corrosion is one of the most pervasive threats, leading to equipment failures, safety risks, and costly downtime. For ships, oil rigs, subsea systems, and coastal infrastructure, implementing robust corrosion prevention strategies for cable assemblies is essential.
Why Corrosion Matters in Marine Cable Assemblies
Corrosion in marine settings occurs due to:
Saltwater exposure: Chlorides in seawater accelerate electrochemical reactions, degrading metals and insulation.
Galvanic corrosion: Dissimilar metals in contact (e.g., copper conductors and steel connectors) create destructive electrical currents.
Humidity and condensation: Moisture ingress weakens insulation and promotes mold or oxidation.
Chemical exposure: Hydrocarbons, acids, and alkalis in offshore drilling or industrial processes degrade materials.
Left unchecked, corrosion can lead to:
Short circuits and electrical fires.
Signal degradation in communication and control systems.
Structural failures in subsea umbilicals or mooring systems.
Key Corrosion Prevention Strategies
1. Material Selection for Corrosion Resistance
Stainless Steel Connectors: Use 316L stainless steel, which contains molybdenum for superior resistance to saltwater and pitting.
Copper Alloys: Opt for tinned or silver-plated copper conductors to prevent oxidation.
High-Performance Jackets:
Polyurethane (PUR): Resists oil, chemicals, and abrasion.
Chlorinated Polyethylene (CPE) or Cross-Linked Polyethylene (XLPE): Withstand UV radiation and saltwater.
Ethylene Propylene Diene Monomer (EPDM): Excellent for temperature extremes (-50°C to 150°C).
2. Protective Coatings and Sealants
Epoxy Coatings: Apply to connectors and terminations to block moisture ingress.
Silicone Gel Sealing: Protects splices and connectors in subsea applications.
Anti-Corrosion Sprays: Use zinc or aluminum-based sprays for metal components.
3. Design Optimization
Galvanic Isolation: Separate dissimilar metals with dielectric barriers (e.g., plastic washers) to prevent galvanic corrosion.
Cathodic Protection: Install sacrificial anodes (e.g., zinc) on subsea cables to divert corrosive currents.
Overmolding and Strain Relief: Reinforce cable entry points with overmolded boots to prevent flex-induced cracks.
4. Environmental Shielding
Armored Cables: Use interlocked aluminum or stainless steel armor for mechanical and corrosion protection.
Conduits and Cable Trays: Deploy corrosion-resistant PVC or fiberglass conduits in high-risk zones.
Maintenance and Monitoring
Regular Inspections: Check for discoloration, pitting, or insulation cracks. Use thermal imaging to detect hotspots caused by corrosion.
Rinsing with Freshwater: Flush salt and contaminants from exposed cables after seawater exposure.
Anti-Corrosion Lubricants: Apply to connectors and joints to repel moisture.
Compliance with Marine Standards
Ensure cable assemblies meet industry-specific certifications, such as:
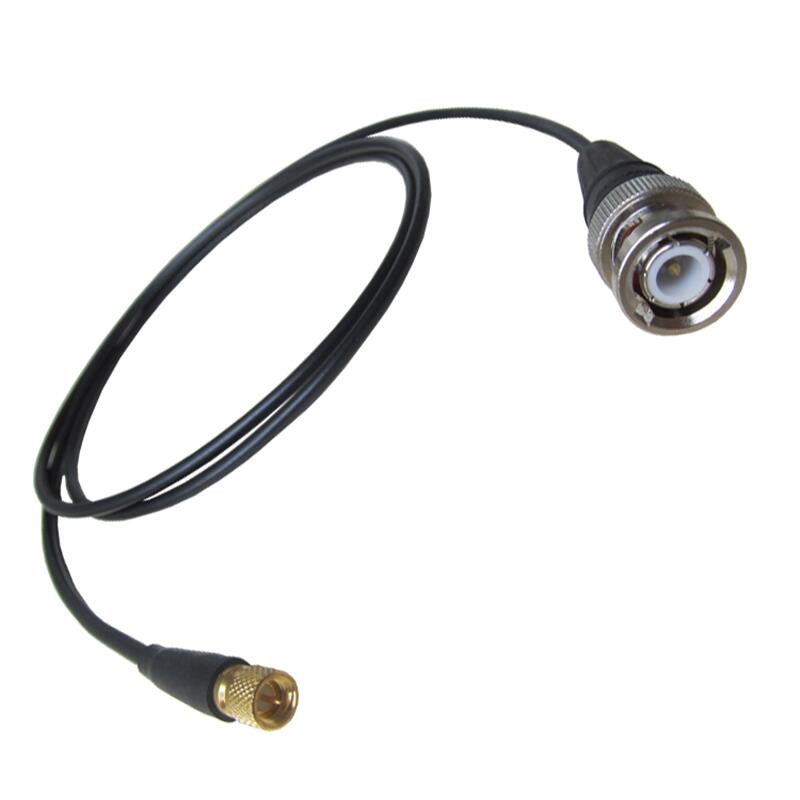
IEC 60092-350/353: Standards for shipboard and offshore power and control cables.
ISO 9224: Corrosion classification for atmospheric environments.
ASTM B117: Salt spray testing requirements.
DNV-GL, ABS, or Lloyds Register: Approval for marine and offshore applications.
Case Study: Subsea Umbilical Cables
Subsea umbilicals, which transmit power, data, and hydraulics to underwater equipment, require multi-layered corrosion protection:
Inner Layers: Tinned copper conductors with XLPE insulation.
Armor: Galvanized steel wires coated with bitumen or polymer.
Outer Sheath: HDPE (high-density polyethylene) for chemical and abrasion resistance.