Cost-Reduction Methods for Standardized Cable Assemblies
In industries ranging from automotive to telecommunications, standardized cable assemblies have become a cornerstone for balancing performance, scalability, and cost efficiency. By minimizing custom designs and consolidating specifications, businesses can achieve significant savings in procurement, inventory, and maintenance.
Why Standardization Drives Cost Savings
Reduced SKU Proliferation: Simplifying designs lowers the number of stock-keeping units (SKUs), streamlining inventory management.
Bulk Purchasing Power: Standardized components (connectors, cables, jackets) enable volume discounts from suppliers.
Lower Testing/Validation Costs: Reusing certified designs eliminates redundant qualification processes.
Simplified Maintenance: Uniform cables reduce training, troubleshooting, and replacement part complexity.
Data Point: A study by the Institute of Electrical and Electronics Engineers (IEEE) found that standardizing 80% of cable assemblies cut procurement costs by 35% and inventory space by 50%.
Key Strategies for Cost-Effective Standardization
1. Component Simplification
Consolidate Connector Types: Replace custom MIL-DTL-38999 variants with widely used M12/M8 connectors for sensors and actuators.
Limit Cable Gauges: Standardize on 3–4 conductor sizes (e.g., 22 AWG for signal, 12 AWG for power) across applications.
Unified Shielding: Adopt a single shielding type (e.g., braided copper) for 90% of assemblies to reduce material complexity.
Case Study: An automotive OEM saved $1.2M annually by replacing 14 custom EV battery harnesses with two standardized designs.
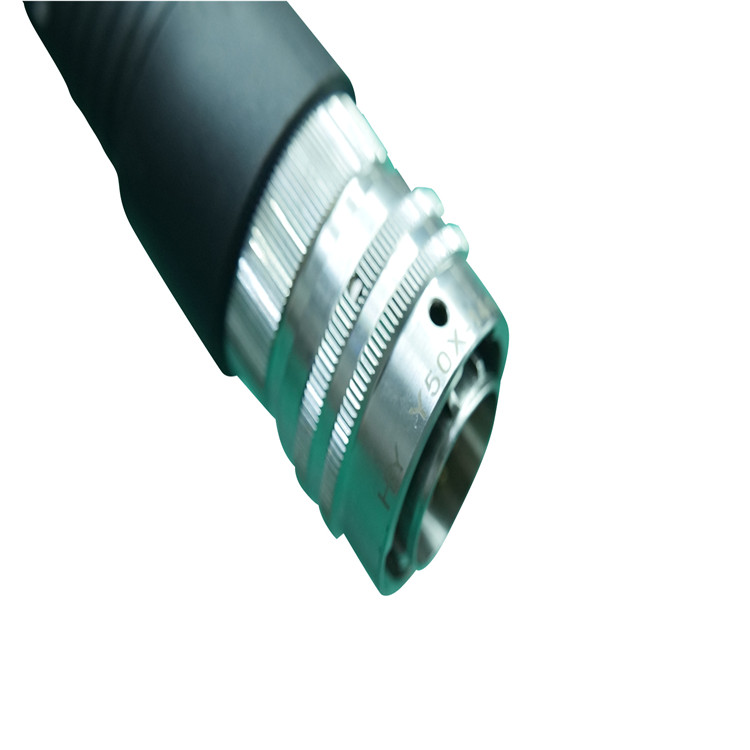
2. Material Standardization
Jacket Materials: Use one UV-resistant material (e.g., PUR) for both indoor and outdoor cables, adjusting only color codes.
Cross-Industry Compliance: Select insulation (e.g., XLPE) that meets multiple standards (UL, IEC, RoHS) to avoid region-specific variants.
Recyclable Options: Standardize on halogen-free, REACH-compliant materials to future-proof against regulatory changes.
3. Design for Manufacturability (DFM)
Modular Designs: Create cable assemblies with interchangeable connectors (e.g., RJ45 to M12 adapters).
Fixed Lengths: Offer cables in 1m increments (e.g., 1m, 2m, 5m) instead of custom lengths to optimize production.
Automated Testing: Design test points compatible with automated continuity and hipot testers.
4. Supplier Collaboration
Joint Development: Partner with suppliers to align standardized specs with their production capabilities.
Long-Term Contracts: Negotiate pricing for multi-year volume commitments on core components.
Dual Sourcing: Qualify two suppliers for critical items (e.g., connectors) to mitigate supply chain risks.
5. Lifecycle Cost Analysis
Total Cost of Ownership (TCO): Factor in maintenance, downtime, and disposal costs when selecting standardized components.
Failure Rate Data: Use historical data to prioritize high-reliability connectors (e.g., circular vs. rectangular).
Example: Switching from custom fiber-optic cables to standardized LC/APC assemblies reduced a data center’s TCO by 28% over 5 years.
Implementation Roadmap
Audit Existing Designs: Identify overlapping specs and high-cost custom parts.
Form a Cross-Functional Team: Include engineering, procurement, and maintenance stakeholders.
Prioritize High-Impact Areas: Focus on assemblies with the highest volume or failure rates.
Pilot Standardized Designs: Test in non-critical systems before full rollout.
Train Teams: Educate staff on new standards and troubleshooting protocols.
Challenges and Mitigation
Performance Trade-offs: Address bandwidth or voltage limitations by reserving custom designs for <10% of critical applications.
Legacy System Compatibility: Use adapters or transition kits to integrate standardized cables with older equipment.
Resistance to Change: Highlight ROI metrics (e.g., 6-month payback periods) to secure buy-in.
Future Trends in Standardization
Digital Twins: Simulate standardized cable performance in virtual environments to optimize designs.
AI-Driven Inventory: Machine learning algorithms predict demand for standardized SKUs, reducing overstock.
Global Standards Harmonization: Initiatives like IEC 61076-2-104 aim to unify connector specs across industries.