Custom vs. Standard Industrial Cable Assemblies: Which Should You Cho...
Industrial cable assemblies are the unsung heroes of modern manufacturing, automation, and infrastructure. They power machinery, transmit critical data, and ensure seamless connectivity in harsh environments. However, selecting the right cable assembly—custom or standard—can significantly impact operational efficiency, safety, and costs. This article explores the differences, advantages, and ideal use cases for custom and standard industrial cable assemblies, empowering businesses to make informed decisions.
Understanding Standard Industrial Cable Assemblies
Standard cable assemblies are pre-designed, mass-produced solutions built to meet common industry requirements. These “off-the-shelf” products are widely available and adhere to established specifications for length, connectors, shielding, and materials.
Advantages of Standard Cable Assemblies
- Cost-Effective: Mass production reduces per-unit costs, making standard assemblies budget-friendly for businesses with straightforward needs.
- Quick Availability: Since they’re stocked by suppliers, standard cables can be shipped immediately, minimizing downtime.
- Proven Reliability: These assemblies are tested across diverse applications, ensuring compliance with industry standards (e.g., UL, RoHS, or IEC).
- Simplified Procurement: No need for lengthy design or testing phases—simply select from a catalog.
Limitations of Standard Assemblies
- Limited Flexibility: They may not fit unique spatial constraints or specialized performance requirements.
- Compromised Performance: In extreme conditions (e.g., high temperatures, corrosive environments), standard cables might underperform.
- Excess Waste: Using longer cables than needed can lead to clutter, maintenance challenges, or signal interference.
Ideal Use Cases for Standard Assemblies
- Repetitive installations (e.g., conveyor systems, HVAC controls).
- Non-critical environments with moderate demands.
- Projects with tight budgets or urgent timelines.
The Case for Custom Industrial Cable Assemblies
Custom cable assemblies are engineered to meet precise specifications, tailored to unique operational needs. From aerospace to oil and gas, industries with demanding conditions often rely on bespoke solutions.
Benefits of Custom Cable Assemblies
- Optimized Performance: Tailored materials (e.g., high-temperature insulation, chemical-resistant jackets) ensure reliability in extreme environments.
- Perfect Fit: Custom lengths and connector configurations eliminate excess wiring, reducing clutter and improving safety.
- Enhanced Durability: Designed for specific stressors (vibration, abrasion, moisture), custom cables often outlast standard options.
- Integrated Features: Add shielding for EMI/RFI protection, hybrid connectors for power+data, or IP-rated seals for waterproofing.
- Scalability: Once designed, custom assemblies can be replicated consistently for large-scale deployments.
Drawbacks of Custom Solutions
- Higher Upfront Costs: Design, prototyping, and testing increase initial investment.
- Longer Lead Times: Development and production may take weeks or months.
- Minimum Order Quantities (MOQs): Some manufacturers require bulk orders.
When to Choose Custom Assemblies
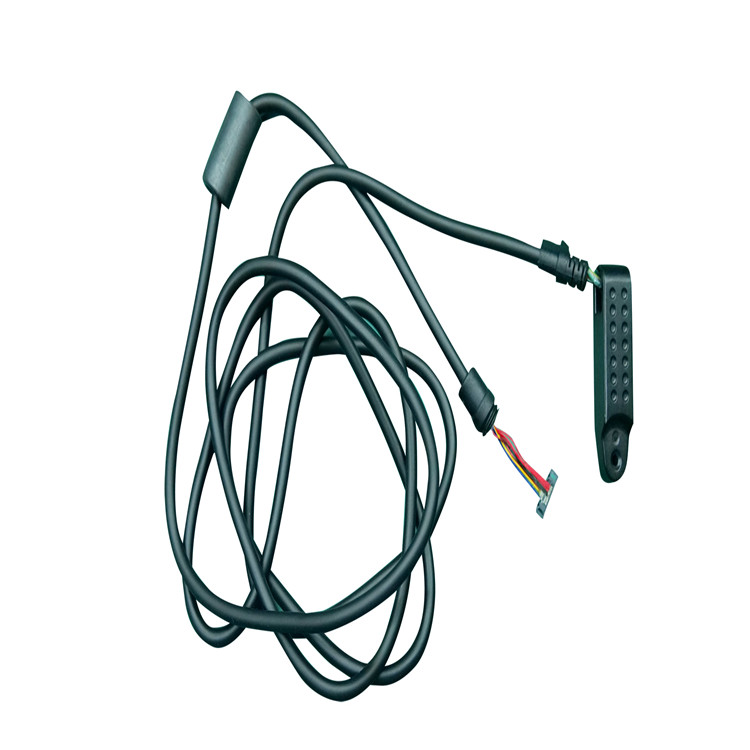
- Critical applications (e.g., medical devices, military systems).
- Harsh environments (extreme temperatures, exposure to chemicals).
- Unique spatial requirements (tight bends, limited panel space).
- Projects requiring future-proofing or scalability.
Key Factors to Guide Your Decision
- Application Requirements:
- Will the cables face extreme temperatures, moisture, or vibrations? → Custom.
- Are you replacing an existing, non-critical component? → Standard.
- Budget Constraints:
- Tight budget with immediate needs? → Standard.
- Higher upfront costs justified by long-term ROI? → Custom.
- Timeline:
- Need a solution within days? → Standard.
- Can accommodate a design phase? → Custom.
- Scalability:
- Planning to expand operations? Custom designs ensure consistency across future installations.
- Regulatory Compliance:
- Industries like automotive or aerospace often require certified custom solutions.
Real-World Examples
Data Centers: Hyperscale facilities often choose custom-length fiber optic cables to optimize airflow and cooling efficiency.
Automotive Manufacturing: A plant upgraded to custom shielded cables to eliminate EMI interference from robotic welders, reducing errors by 30%.
Renewable Energy: A solar farm used standard UV-resistant cables for routine connections but opted for custom waterproof assemblies in flood-prone areas.