Customized Cable Assemblies for Smart Factories: Boost Efficiency &am...
In the era of Industry 4.0, smart factories are redefining manufacturing with automation, IoT integration, and data-driven processes. However, achieving seamless connectivity and operational efficiency hinges on a critical yet often overlooked component: customized cable assemblies. Tailored to meet the unique demands of modern industrial environments, these specialized solutions are the backbone of reliable communication, power distribution, and system integration. In this article, we’ll explore how custom cable assemblies optimize smart factories, improve productivity, and ensure future-ready connectivity.
Why Smart Factories Need Customized Cable Assemblies
Smart factories rely on interconnected systems—robotics, sensors, PLCs, and cloud platforms—to operate efficiently. Off-the-shelf cables often fall short in addressing the complexity of these setups. Here’s why customization matters:
- Precision Compatibility
Standard cables may not align with the voltage, current, or signal requirements of advanced machinery. Custom assemblies are engineered to match exact specifications, minimizing signal loss, electromagnetic interference (EMI), and power inefficiencies. - Space Optimization
Smart factories prioritize compact layouts. Custom cables can be designed with specific lengths, bend radii, and connector types to fit tight spaces, reducing clutter and simplifying maintenance. - Durability in Harsh Environments
Industrial settings expose cables to extreme temperatures, chemicals, vibrations, and abrasion. Custom assemblies use ruggedized materials like shielded jackets, high-temperature insulation, and waterproof connectors to ensure longevity. - Scalability
As factories adopt new technologies, cable systems must adapt. Custom solutions allow for modular designs, making upgrades or expansions faster and cost-effective.
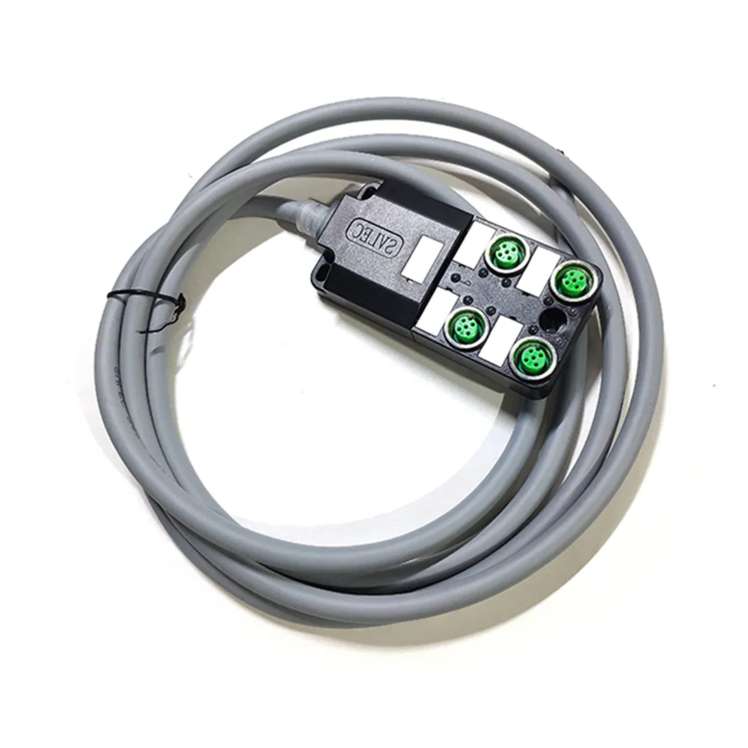
Key Applications of Custom Cable Assemblies in Smart Factories
From assembly lines to quality control, customized cables play a pivotal role in key areas:
- Industrial Robotics
Robotic arms and AGVs (Automated Guided Vehicles) require flexible, high-speed cables to handle constant movement and data transmission. Custom assemblies with torsion-resistant designs ensure uninterrupted operation. - IoT Sensors and Edge Devices
Sensors collecting real-time data need reliable connections. Shielded cables with noise-resistant properties maintain signal integrity, enabling accurate analytics and predictive maintenance. - High-Speed Data Networks
Fiber-optic or Cat6/7 Ethernet cables customized for low latency support real-time communication between machines, ERP systems, and cloud platforms. - Power Distribution Systems
Heavy-duty power cables with high ampacity ratings safely deliver electricity to motors, drives, and machinery, reducing downtime from overloads.
5 Benefits of Investing in Custom Cable Solutions
- Enhanced Operational Efficiency
Minimize downtime caused by cable failures or mismatches. Custom assemblies ensure systems run smoothly, maximizing throughput. - Cost Savings Over Time
While initial costs may be higher, durable custom cables reduce replacement and maintenance expenses. - Future-Proofing
Design cables with spare conductors or modular connectors to accommodate future tech upgrades. - Compliance with Industry Standards
Meet certifications like UL, RoHS, or ISO for safety and global market access. - Improved Safety
Flame-retardant or explosion-proof cables mitigate risks in hazardous environments.
How to Choose the Right Custom Cable Assembly Partner
Not all suppliers can deliver high-performance solutions. Look for these qualities:
- Expertise in Industrial Applications: Experience with robotics, automation, and IoT systems.
- In-House Engineering Support: Ability to prototype and test designs under real-world conditions.
- Quality Assurance: Rigorous testing for EMI resistance, flex life, and environmental resilience.
- Fast Turnaround Times: Scalable production to meet urgent deadlines without compromising quality.
Future Trends Driving Demand for Custom Cables
Sustainable Manufacturing: Eco-friendly materials like recyclable sheaths are gaining traction.
5G and Edge Computing: Ultra-low latency networks require high-frequency, shielded cables.
AI-Driven Manufacturing: Advanced analytics demand robust data transmission capabilities.