Key Differences Between Industrial Cables and Household Cables
When selecting electrical cables for a project, understanding the differences between industrial cables and household cables is critical. These two cable types are designed for distinct environments, safety requirements, and performance standards. This guide breaks down their differences in materials, construction, applications, and safety features to help users make informed decisions.
1. Purpose and Application Environment
Industrial Cables:
- Designed for harsh environments like factories, mining sites, oil refineries, and power plants.
- Handle extreme temperatures (-50°C to 200°C), moisture, chemicals, and mechanical stress (abrasion, crushing).
- Used in high-voltage systems (up to 35 kV or more) for machinery, motors, and heavy equipment.
Household Cables:
- Built for residential settings with stable, low-risk conditions (indoors or protected outdoor areas).
- Operate in moderate temperatures (typically -20°C to 60°C).
- Power everyday appliances, lighting, and low-voltage systems (up to 600 V).
2. Material and Construction
Industrial Cables:
- Conductors: Use high-purity copper or aluminum for superior conductivity and heat resistance.
- Insulation: Robust materials like cross-linked polyethylene (XLPE) or thermoplastic elastomers (TPE) to resist heat, oils, and UV radiation.
- Shielding: Often include metal braids or foil to block electromagnetic interference (EMI) in industrial settings.
- Armoring: Steel or aluminum armor protects against physical damage.
Household Cables:
- Conductors: Standard copper or aluminum (less stringent purity requirements).
- Insulation: PVC (polyvinyl chloride) is common for its flexibility and cost-effectiveness.
- Shielding: Rarely shielded unless for specific applications (e.g., Ethernet cables).
- Jacketing: PVC or thermoplastic covers for basic protection.
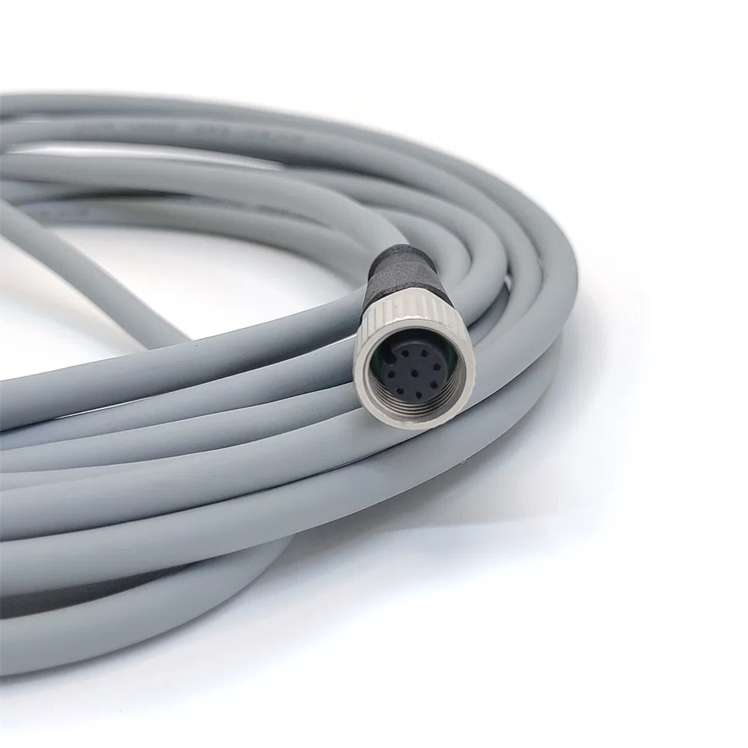
3. Voltage and Current Capacity
Industrial Cables:
- Rated for higher voltage levels (1 kV to 35 kV) to support heavy machinery and three-phase power systems.
- Handle continuous high current loads without overheating.
Household Cables:
- Designed for low-voltage applications (120 V to 600 V) typical in homes.
- Current capacity aligns with residential needs (e.g., 15–20 amps for outlets).
4. Safety and Compliance Standards
Industrial Cables:
- Must meet rigorous certifications like UL 1277, IEC 60502, or NEC Article 310 for hazardous locations.
- Flame-retardant and fire-resistant materials (e.g., LSZH – Low Smoke Zero Halogen) to prevent toxic fumes in fires.
Household Cables:
- Complies with residential safety standards like UL 83 (for building wires) and NEC Article 334.
- Focus on preventing short circuits and electric shocks rather than extreme conditions.
5. Durability and Lifespan
Industrial Cables:
- Built to last 20–30 years under constant stress.
- Resistant to degradation from chemicals, oils, and repetitive flexing.
Household Cables:
- Average lifespan of 10–20 years in stable environments.
- Less durable under mechanical strain or exposure to harsh elements.
6. Cost Considerations
Industrial Cables:
- Higher upfront cost due to advanced materials, shielding, and certifications.
- Long-term savings from reduced downtime and maintenance.
Household Cables:
- Affordable and widely available, optimized for budget-friendly residential use.
7. Common Types of Cables
Industrial Cable Examples:
- Instrumentation cables (for signal transmission).
- Power control cables (for motors and transformers).
- Armored cables (e.g., SWA – Steel Wire Armored).
Household Cable Examples:
- NM-B cables (Romex®) for indoor wiring.
- Coaxial cables (TV/internet).
- Speaker wires and low-voltage lighting cables.
Why You Should Never Interchange Them
Using household cables in industrial settings risks overheating, fires, or equipment failure. Conversely, industrial cables in homes are unnecessarily expensive and harder to install due to stiffness.
Choosing the Right Cable: A Checklist
- Environment: Will the cable face moisture, heat, or chemicals?
- Voltage: Match the cable’s rating to your system’s needs.
- Certifications: Ensure compliance with local safety standards.
- Flexibility: Industrial settings may require frequent bending.