High-Voltage Cable Assembly Solutions for the Oil and Gas Industry
Introduction
The oil and gas industry operates in some of the most demanding environments on Earth—offshore platforms, subsea installations, and remote drilling sites—where extreme pressures, corrosive substances, and temperature fluctuations are commonplace. High-voltage cable assemblies in these settings must deliver uninterrupted power and signal transmission while enduring harsh conditions. This article explores the critical requirements, advanced materials, and innovative designs that define reliable high-voltage cable solutions for oil and gas applications, ensuring safety, efficiency, and compliance with stringent industry standards.
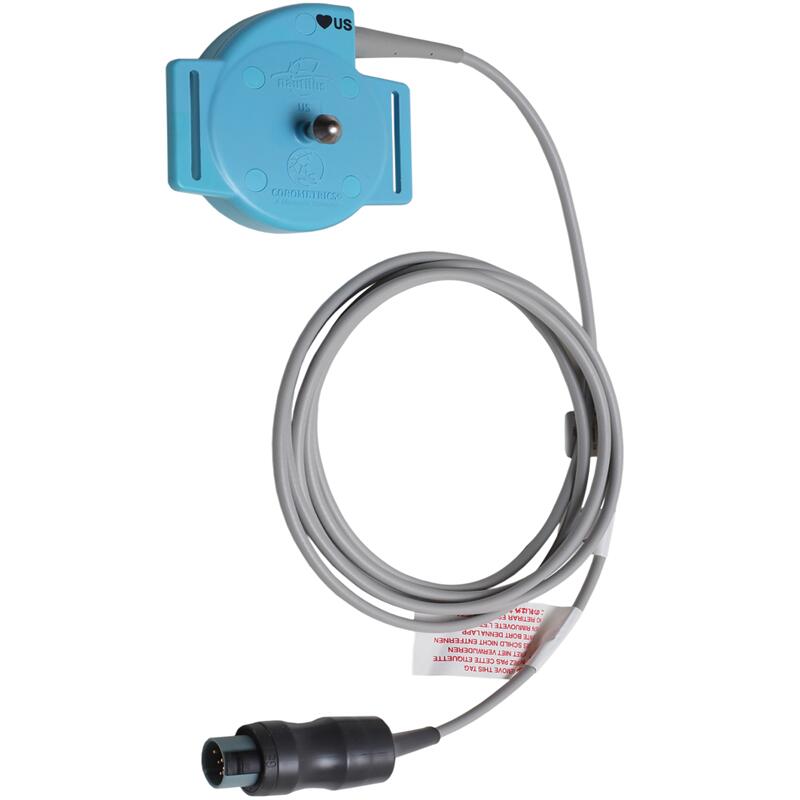
Key Challenges in Oil and Gas Environments
High Pressure and Temperature: Subsea cables face pressures exceeding 300 bar and temperatures up to 150°C.
Chemical Exposure: Resistance to hydrocarbons, H₂S, seawater, and drilling fluids is essential.
Mechanical Stress: Abrasion, crushing, and repeated bending in dynamic applications like offshore rigs.
Electrical Safety: Preventing arcing, short circuits, and insulation breakdown in high-voltage systems (1–36 kV).
Longevity: Cables must operate reliably for decades with minimal maintenance in inaccessible locations.
Critical Requirements for High-Voltage Cable Assemblies
1. Robust Insulation and Sheathing Materials
Cross-Linked Polyethylene (XLPE):
Withstands high voltages (up to 36 kV) and temperatures (90°C to 130°C).
Resists electrical treeing and thermal degradation.
Ethylene Propylene Rubber (EPR):
Flexible and resistant to ozone, ideal for dynamic offshore applications.
Chlorosulfonated Polyethylene (CSPE):
Excellent chemical resistance for onshore refineries and pipelines.
Lead or Aluminum Barriers:
Moisture and gas ingress protection for subsea cables.
2. Mechanical Durability
Armored Designs:
Steel wire armoring (SWA) or interlocked metal tapes for crush resistance in subsea trenches.
Aramid Fiber Reinforcement:
Lightweight yet strong tensile layers for deep-water riser cables.
Abrasion-Resistant Jackets:
Polyurethane (PUR) or chlorinated polyethylene (CPE) for surface equipment.
3. Chemical and Corrosion Resistance
Fluoropolymer Layers:
PTFE or PFA coatings protect against acidic gases (e.g., H₂S) and hydrocarbons.
Stainless Steel Components:
Corrosion-resistant connectors and glands for offshore environments.
4. Safety and Compliance
Flame Retardancy:
Low-smoke zero-halogen (LSZH) materials prevent toxic fumes in confined spaces.
Explosion-Proof Certification:
ATEX/IECEx compliance for cables used in hazardous zones (Zone 1/2).
Subsea Standards:
Compliance with API 17J for dynamic umbilicals and IEC 60502 for offshore power cables.
Specialized Cable Solutions for Oil and Gas Applications
1. Subsea Power Cables
Application: Powering subsea pumps, Christmas trees, and control systems.
Design:
Triple extrusion (conductor, XLPE insulation, lead sheath) with armoring.
Integrated fiber optics for real-time monitoring.
Standards: IEEE 1580, IEC 60840.
2. Drilling Rig Cables
Application: Hoisting systems, top drives, and blowout preventers (BOPs).
Design:
High-flex EPR insulation with PUR jackets.
Torsion-resistant conductors for vertical movement.
3. Downhole Cables
Application: Logging tools and electric submersible pumps (ESPs).
Design:
Slim-diameter cables with PTFE insulation for high-temperature wells.
Metal-sealed connectors rated for 20,000 psi.
4. Umbilicals and Composite Cables
Application: Hydraulic, electrical, and chemical supply in subsea systems.
Design:
Multi-core bundles with HDPE sheathing and steel tubes.
Dynamic fatigue resistance for wave-induced motion.
Case Study: High-Voltage Cables in Offshore Wind-to-Oil Projects
Challenge: A North Sea operator needed cables to connect offshore wind farms to oil platforms, requiring resistance to saltwater, high voltage (33 kV), and dynamic seabed movement.
Solution:
Cable Design: XLPE-insulated submarine cables with double-armored steel layers and HDPE anti-fouling coating.
Integration: Fiber-optic sensors for strain and temperature monitoring.
Result: Reduced downtime by 30% and extended service life to 25+ years.
Emerging Trends in Oil and Gas Cable Technology
Smart Monitoring Systems:
Embedded sensors for predictive maintenance, detecting insulation wear or thermal hotspots.
High-Temperature Superconductors (HTS):
Reducing energy loss in long-distance subsea transmission.
Eco-Friendly Materials:
Recyclable sheathing and bio-based polymers to meet environmental regulations.
Modular Connectors:
Quick-deploy solutions for remote drilling sites.