How to Ensure Cable Assembly Physical Properties Meet Industry Standa...
1.Material Selection and Compliance
a. Conductors:
Standards: IEC 60228 (conductor classes) defines cross-sectional areas and resistance tolerances.
Best Practices:
Use high-purity copper (≥99.95%) to minimize resistivity.
For flexibility, adopt fine-stranded conductors (e.g., Class 5 or 6 per IEC 60228).
b. Insulation and Jacketing:
Standards: UL 444 (communications cables), UL 1685 (vertical tray flame test).
Material Choices:
Flame Retardancy: Cross-linked polyethylene (XLPE) or LSZH (Low Smoke Zero Halogen) materials meet IEC 60332-1 flame tests.
Flexibility: Thermoplastic elastomers (TPE) or silicone for dynamic applications.
c. Shielding and Armor:
Standards: IEC 61196 (coaxial cables), ASTM B736 (corrosion-resistant coatings).
Design:
Braided copper shields for EMI/RFI protection (≥85% coverage for industrial use).
Galvanized steel armor (ISO 6722 for automotive cables) for mechanical protection.
2. Design Validation Through Simulation
a. Finite Element Analysis (FEA):
Simulate mechanical stresses (bending, tension, torsion) to optimize geometry and material distribution.
Example: ANSYS Mechanical for predicting fatigue life in robotic cables.
b. Thermal Modeling:
Assess heat dissipation in high-current cables to prevent insulation degradation (e.g., IEC 60502-2 for power cables).
3. Rigorous Testing Protocols
Key Physical Tests and Standards:
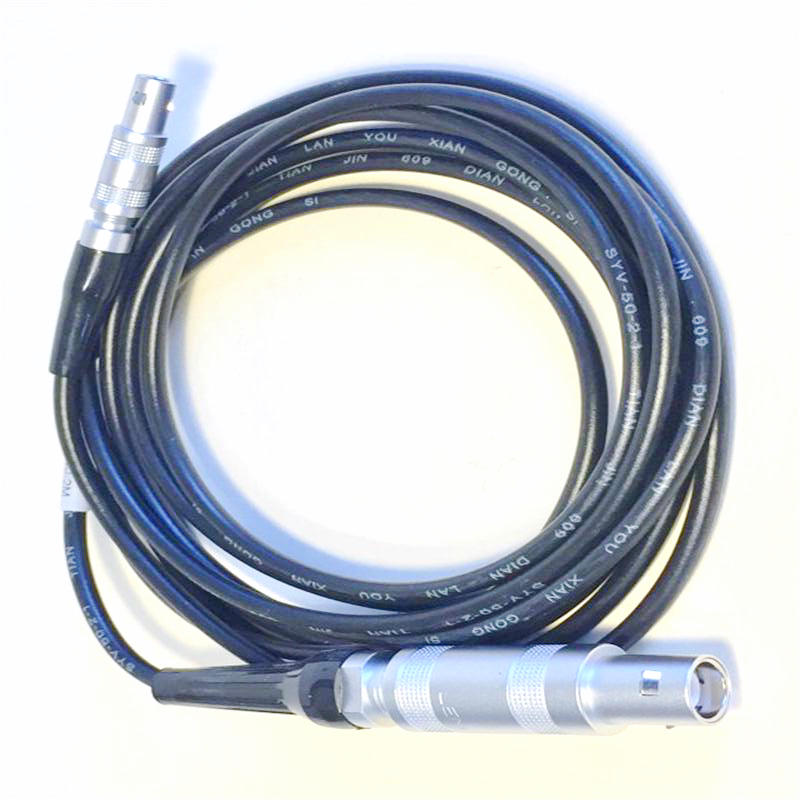
Property Test Method Standard Acceptance Criteria
Tensile Strength Tensile testing machine ASTM D638 ≥12 MPa (TPU jackets)
Flexibility Repeated bending cycles IEC 61158-2 (500k cycles) No cracks or conductor breaks
Flame Resistance Vertical flame test UL 1685 Char length ≤1.5 m, no flaming drops
Abrasion Taber Abraser test ISO 6722 ≤100 mg loss after 1,000 cycles
Environmental Salt spray, UV exposure ASTM B117, IEC 60068-2-5 No corrosion/insulation cracks after 720h
Testing Best Practices:
Third-Party Certification: Use accredited labs (e.g., TÜV, Intertek) for unbiased validation.
Batch Sampling: Test 5-10% of production batches per ISO 2859-1 (AQL sampling).
4. Manufacturing Process Control
a. Extrusion Consistency:
Monitor insulation/jacket thickness (±0.1 mm tolerance) via laser micrometers.
Ensure concentricity (≤10% eccentricity per IEC 60754-1).
b. Stranding and Twisting:
Automated stranding machines maintain lay length consistency (e.g., 10-15x cable diameter).
Prevent “birdcaging” in shielded cables with proper tension control.
c. Termination and Sealing:
Overmold connectors with IP67/IP68-rated materials (e.g., silicone) to prevent ingress.
Validate crimp strength via pull tests (e.g., 50N minimum for signal cables).
5. Compliance Documentation and Traceability
Material Certificates: Obtain COPP (Certificates of Plastic Properties) and RoHS/REACH compliance reports.
Traceability Systems: Implement barcoding or RFID tagging per IEC 62491 to track batches from raw material to end product.
Case Study: Automotive High-Voltage Cables
Challenge: A supplier needed cables compliant with LV214 (automotive) for electric vehicles.
Solution:
Material: Silicone insulation (175°C rating) + TPE jacket.
Testing: Passed 3,000-hour thermal aging (ISO 6722) and 50N/mm² tensile tests.
Certification: Achieved LV214-2 and ISO 19642 validation.
Emerging Tools for Quality Assurance
AI-Driven Inspection:
Machine learning algorithms detect micro-cracks or voids in real-time X-ray scans.
Smart Cables with Embedded Sensors:
Fiber Bragg gratings (FBG) monitor strain and temperature during operation.
Blockchain for Supply Chain Transparency:
Immutable records of material sourcing and test results (e.g., IBM Food Trust adapted for cables).