How to Evaluate the ROI of Standardized Cable Assemblies
Standardized cable assemblies are a cornerstone of efficient manufacturing and product design, offering consistency, reduced lead times, and cost predictability. However, quantifying their return on investment (ROI) is critical for businesses to justify the shift from custom solutions. This guide breaks down the key steps to evaluate ROI accurately, ensuring you make data-driven decisions.
1. Define the Scope of Your Evaluation
Start by identifying the specific applications where standardized cable assemblies will be used. For example:
- Product lines: Which devices or systems will incorporate these assemblies?
- Volume: Estimate annual production quantities.
- Current costs: Calculate expenses tied to custom cable design, prototyping, testing, and inventory management.
This baseline helps isolate the financial impact of switching to standardized solutions.
2. Calculate Direct Cost Savings
Standardized cable assemblies eliminate several costs associated with custom designs:
- Design and prototyping: Save 5,000–15,000 per project by avoiding custom CAD work and prototype iterations.
- Material costs: Bulk purchasing of standardized components reduces per-unit material costs by 20–40%.
- Labor efficiency: Reduce assembly time by 30–50% with pre-engineered solutions that require less manual labor.
Formula for direct savings:
(Current cost per unit − Standardized cost per unit) × Annual production volume
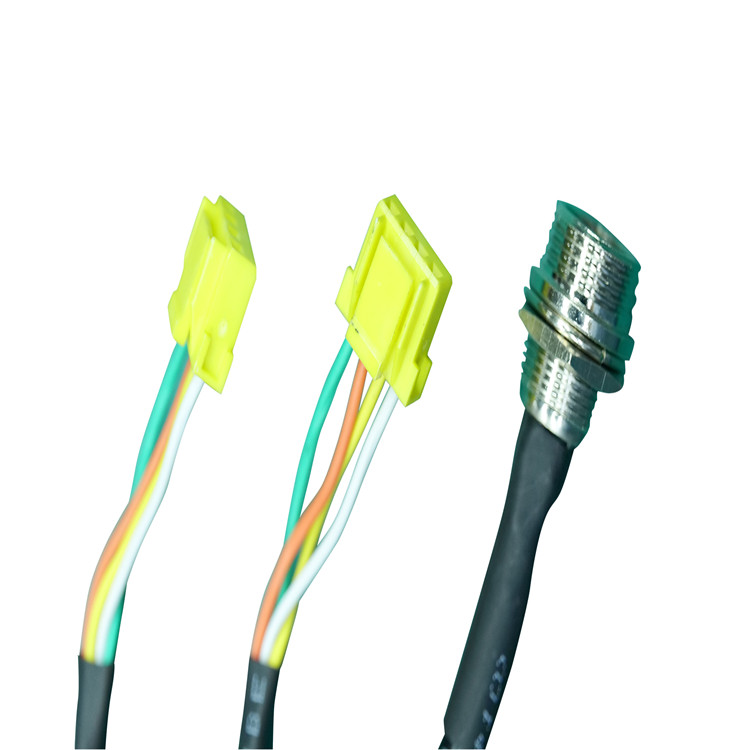
3. Factor in Indirect Savings
Beyond direct costs, standardized assemblies drive operational efficiencies:
- Reduced downtime: Pre-tested assemblies minimize failures, cutting maintenance costs by up to 25%.
- Simplified inventory: Lower SKU counts decrease warehousing expenses and reduce stockouts.
- Faster time-to-market: Eliminate 4–8 weeks of design lead time, accelerating product launches.
Example: A medical device manufacturer reduced downtime by 20% after switching to standardized assemblies, saving $200,000 annually in service calls.
4. Quantify Quality and Reliability Benefits
Standardized cables are rigorously tested for compliance (e.g., UL, ISO), reducing the risk of defects. This translates to:
- Lower warranty claims: A 15–30% reduction in field failures.
- Enhanced brand reputation: Fewer recalls or returns improve customer trust and retention.
5. Assess Long-Term Flexibility
Standardized solutions future-proof your operations:
- Scalability: Easily ramp production up or down without redesign costs.
- Cross-compatibility: Use the same assembly across multiple products, reducing R&D spend.
Case study: An automotive supplier saved $1.2M over three years by using one standardized harness across five vehicle models.
6. Use a Total Cost of Ownership (TCO) Model
ROI isn’t just about upfront savings—it’s about lifetime value. Compare the TCO of standardized vs. custom cables over 3–5 years, including:
- Acquisition costs
- Maintenance and repair
- Scrap/waste rates
- Opportunity costs (e.g., delayed launches)
7. Leverage Industry Benchmarks
Compare your ROI projections with industry averages:
- Electronics manufacturers typically achieve 12–18-month payback periods.
- Aerospace/defense sectors see 25–35% cost reductions due to stringent compliance requirements.
Final Formula for ROI Calculation
ROI (%) = [(Total Savings − Total Investment) / Total Investment] × 100
Example:
- Total investment: $50,000 (tooling, training, initial inventory)
- Annual savings: $75,000 (direct + indirect)
- ROI: [(75,000 − 50,000) / 50,000] × 100 = 50% ROI in Year 1