Maintenance Tips to Extend the Lifespan of Industrial Cable Assembli...
Industrial cable assemblies are critical for powering machinery, transmitting data, and ensuring seamless operations in sectors like manufacturing, energy, and automation. However, harsh environments—such as extreme temperatures, vibration, and chemical exposure—can degrade cables over time, leading to failures and costly downtime. Proactive maintenance is key to maximizing their lifespan and reliability.
1. Regular Inspections: Catch Issues Early
Why It Matters: Minor abrasions, loose connectors, or corrosion can escalate into major failures if ignored.
Checklist:
Visual Inspections: Look for cracks, fraying, or discoloration in insulation/jackets.
Connector Integrity: Ensure pins are clean, undamaged, and securely mated.
Shielding Damage: Check for cuts or gaps in foil/braided shields (common in high-EMI areas).
Bend Radius Compliance: Verify cables aren’t kinked beyond the manufacturer’s specified radius.
Frequency:
Monthly: For cables in high-stress zones (e.g., robotic arms, moving conveyors).
Quarterly: For static installations (control panels, fixed sensors).
2. Proper Cleaning and Contamination Control
Why It Matters: Dust, oil, and moisture accelerate corrosion and insulation breakdown.
Best Practices:
Non-Abrasive Cleaning: Use lint-free cloths and isopropyl alcohol to wipe connectors. Avoid harsh chemicals.
Seal Protection: Reapply dielectric grease to IP-rated connectors after cleaning to maintain water resistance.
Cable Trays/Conduits: Route cables away from coolant sprays, metal shavings, or chemical drips.
Case Study: A food processing plant reduced cable replacements by 50% after implementing weekly cleaning of PUR-jacketed cables exposed to steam and grease.
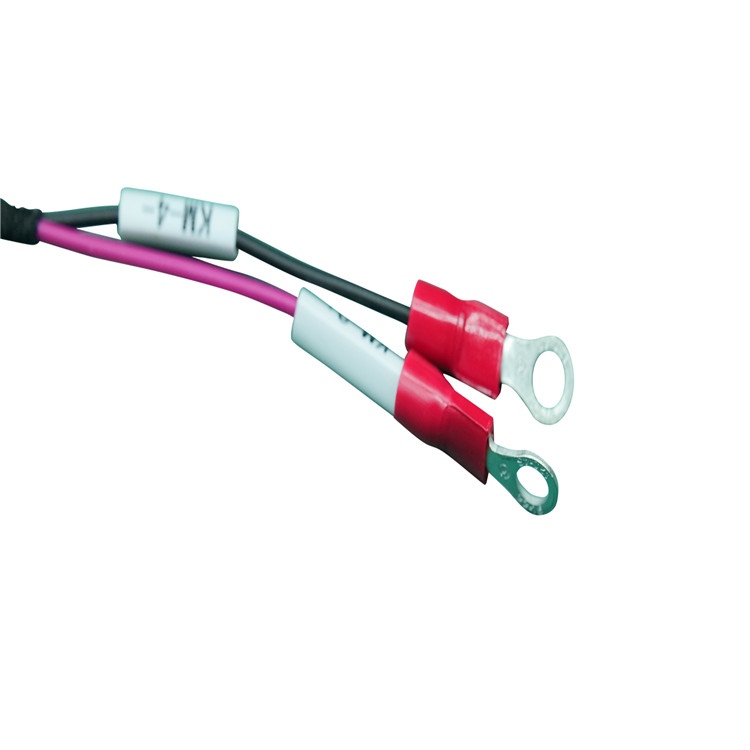
3. Strain Relief and Physical Protection
Why It Matters: Tension, vibration, and repetitive motion can fatigue conductors and connectors.
Solutions:
Cable Carriers (e.g., Drag Chains): Guide and protect cables in dynamic applications like CNC machines.
Strain Relief Boots: Install at connector junctions to prevent bending stress.
Zip Tie Caution: Avoid over-tightening, which can compress insulation. Use Velcro straps for adjustable bundling.
Pro Tip: For robotic arms, use cables rated for ≥5 million flex cycles.
4. Environmental Management
Why It Matters: Temperature extremes, UV exposure, and humidity degrade materials over time.
Mitigation Strategies:
Thermal Protection: Use silicone-jacketed cables (>150°C) near furnaces or welding stations.
UV Resistance: Opt for black LDPE jackets in outdoor solar or wind installations.
Moisture Control: Deploy pressurised conduits or desiccant bags in humid environments.
Data Point: Teflon-insulated cables last 3× longer than PVC in chemical plants due to superior acid resistance.
5. Labeling and Documentation
Why It Matters: Poor documentation leads to mismatched replacements or incorrect handling during repairs.
Best Practices:
Color Coding: Assign colors by voltage (e.g., red for 480V, yellow for 24V DC).
QR Code Tags: Link to digital specs (length, gauge, shielding type) for quick scanning.
Maintenance Logs: Track inspection dates, issues found, and corrective actions.
6. Upgrade Outdated Components
Why It Matters: Older cables may lack modern materials or shielding needed for today’s high-speed IIoT systems.
Signs You Need an Upgrade:
Frequent EMI-induced data errors.
Incompatibility with new machinery (e.g., legacy RJ45 vs. M12-D-coded Ethernet).
Insulation hardening or brittleness.
Smart Swaps:
Replace PVC with TPE jackets for flexibility.
Upgrade Cat5e to Cat6A for 10Gbps+ bandwidth.
Use hybrid fiber-copper cables for long-distance, noise-immune power+data transmission.
Case Study: Steel Mill Cable Lifespan Doubled
A steel mill faced recurring failures of motor power cables due to extreme heat and slag exposure. After implementing:
Ceramic-coated cables for thermal protection.
Bi-annual infrared scans to detect hotspots.
Preventive replacement schedules based on wear trends.
Result: Cable lifespan increased from 1.5 to 3 years, saving $120k annually.
Emerging Technologies for Predictive Maintenance
Smart Cables: Embedded sensors monitor temperature, strain, or impedance in real time.
AI Analytics: Platforms like Siemens MindSphere predict failures using historical performance data.
Robotic Inspectors: Drones or crawlers inspect overhead or hard-to-reach cables in oil rigs.