Technical Requirements and Standards for Industrial Cable Assemblies
- Electrical Performance: Powering Precision
1.1 Voltage and Current Ratings
Industrial cable assemblies are categorized by voltage classes:
Low Voltage (LV): Up to 1,000V AC / 1,500V DC for robotics, PLCs, and conveyor systems.
Medium Voltage (MV): 1 kV–35 kV for mining equipment, wind turbines, and substations.
High Voltage (HV): 35 kV–230 kV for grid infrastructure and heavy machinery.
Key Standards:
IEC 60502-2: Defines MV cable testing for 6–30 kV systems.
UL 44: Rubber-insulated wires for 600V–2,000V applications.
1.2 EMI/RFI Shielding
Electromagnetic interference (EMI) and radio-frequency interference (RFI) can disrupt sensitive equipment. Solutions include:
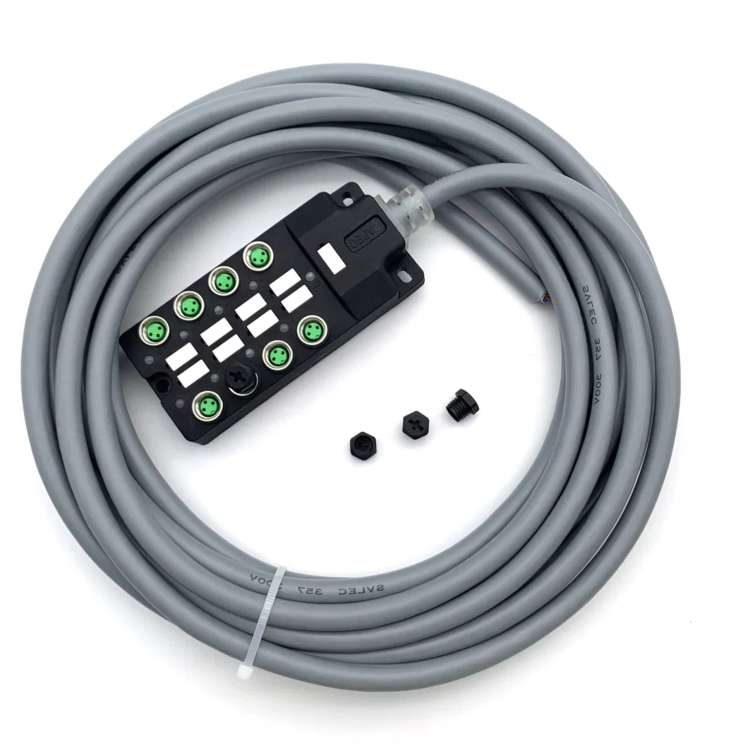
Copper Braided Shields: 85–95% coverage for motors and VFDs.
Foil Shielding: Aluminum-polyester layers for high-frequency noise suppression.
Standards: EN 50289-1-6 (EMC testing), MIL-DTL-17 (military-grade shielding).
2. Mechanical and Physical Durability
2.1 Flexibility and Bend Radius
Dynamic Applications: Minimum bending radius ≥ 8× cable diameter (e.g., robotic arms).
Tensile Strength: ≥50 N/mm² for drag chains and reeling systems.
2.2 Abrasion and Crush Resistance
Jacket Materials: Polyurethane (PU) for oil resistance; TPE for flexibility.
Test Standards:
IEC 60227-1: Mechanical stress tests for PVC-insulated cables.
UL 1277: Crush resistance for tray cables.
3. Environmental Resilience
3.1 Temperature Tolerance
Operating Range: -50°C to 200°C, with silicone or XLPE insulation.
Cold Flexibility: Passes IEC 60811-504 (-40°C bend tests).
3.2 Chemical and Weather Resistance
Oil/Grease Resistance: Chloroprene rubber (CPE) jackets per UL 44.
UV Stability: Cross-linked polyethylene (XLPE) for outdoor use (e.g., solar farms).
3.3 Water and Dust Protection
IP Ratings: IP67/IP69K seals for washdown environments (food processing, marine).
Submersion Tests: IEC 60529 validation for underwater applications.
4. Safety and Compliance Standards
4.1 Flame Retardancy
Vertical Flame Tests: IEC 60332-1-2 (single cable) and IEC 60332-3-24 (bundled cables).
Low Smoke Zero Halogen (LSZH): Complies with IEC 60754 for toxic gas emissions.
4.2 Certifications by Region
Region Key Standards Focus Area
North America UL 44, NEC Article 310 Fire safety, ampacity tables
Europe EN 50575, ATEX Directive Hazardous environments
Asia GB/T 9330, JIS C 3306 Industrial automation
5. Installation and Maintenance Best Practices
5.1 Routing and Fixation
Separation: Maintain ≥300 mm between power and data cables to prevent interference.
Cable Trays: Use corrugated trays (per NEMA VE-1) for heat dissipation.
5.2 Predictive Maintenance
Thermal Imaging: Detect hotspots caused by overloads or insulation wear.
Partial Discharge Testing: Monitor HV cables for dielectric breakdown risks.
6. Case Study: Automotive Manufacturing Plant
Challenge: Frequent cable failures in robotic welding cells due to heat and mechanical stress.
Solution:
Installed 200°C-rated silicone cables with a bend radius of 10× diameter.
Implemented EMI-shielded trays to protect CAN bus communication lines.
Result: 60% reduction in downtime; compliance with ISO 6722 automotive standards.
7. Future Trends in Industrial Cable Assemblies
Smart Cables: IoT-enabled assemblies with embedded sensors for real-time health monitoring.
Sustainable Materials: Bio-based polymers and recyclable LSZH compounds.