Top 10 Performance Metrics for Industrial Cable Harnesses: An Enginee...
Meta Description: Discover the critical performance metrics for industrial cable harnesses—from voltage rating to flex life—and learn how to evaluate quality for reliability and safety.
Table of Contents
Why Performance Metrics Matter
Top 10 Metrics to Evaluate
2.1 Voltage Rating
2.2 Current Capacity (Ampacity)
2.3 Temperature Range
2.4 Flex Life (Bend Cycles)
2.5 Tensile Strength
2.6 Chemical Resistance
2.7 IP (Ingress Protection) Rating
2.8 EMI/RFI Shielding Effectiveness
2.9 Flammability Rating (UL 94)
2.10 Conductor Resistance
How to Test These Metrics
Case Study: Avoiding Failure in Automotive Robotics
FAQs
Conclusion & Resources
1. Why Performance Metrics Matter
Industrial cable harnesses are the lifelines of machinery in sectors like manufacturing, energy, and automation. A single weak link—such as a corroded connector or undersized conductor—can lead to system failures, costly downtime, or safety hazards. By rigorously evaluating these 10 metrics, engineers ensure cables meet operational demands and comply with industry standards.
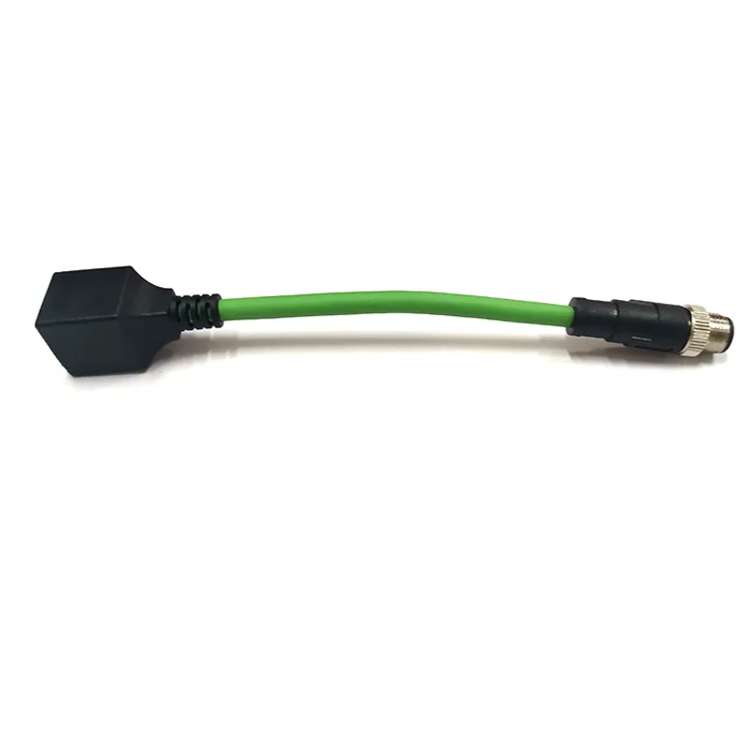
2. Top 10 Metrics to Evaluate
2.1 Voltage Rating
What It Measures: Maximum safe voltage the cable can handle.
Why It Matters: Exceeding voltage limits risks insulation breakdown and short circuits.
Standards: IEC 60502-1 for power cables.
Example: A 600V-rated cable for CNC machines vs. 1kV for wind turbines.
2.2 Current Capacity (Ampacity)
What It Measures: Maximum continuous current without overheating.
Why It Matters: Overloaded cables degrade insulation and cause fires.
Testing: Follow NEC Table 310.16 for ambient temperature adjustments.
2.3 Temperature Range
What It Measures: Operating temperature limits (e.g., -40°C to 105°C).
Why It Matters: Extreme heat softens insulation; cold makes jackets brittle.
Materials: Silicone (high-temp) vs. PVC (moderate-temp).
2.4 Flex Life (Bend Cycles)
What It Measures: Number of bend cycles before failure.
Why It Matters: Critical for robotic arms, drag chains, and moving machinery.
Benchmark: 10 million cycles for high-flex applications.
2.5 Tensile Strength
What It Measures: Resistance to pulling force (measured in Newtons).
Why It Matters: Prevents cable damage during installation or vibration.
Standard: UL 1581 tensile test.
2.6 Chemical Resistance
What It Measures: Durability against oils, acids, and solvents.
Why It Matters: Essential for chemical plants, food processing, and offshore rigs.
Materials: Teflon® (FEP) for aggressive environments.
2.7 IP (Ingress Protection) Rating
What It Measures: Protection against dust and water (e.g., IP67, IP69K).
Why It Matters: IP67 ensures survival in dusty warehouses; IP69K withstands high-pressure washdowns.
2.8 EMI/RFI Shielding Effectiveness
What It Measures: Ability to block electromagnetic/radio frequency interference.
Why It Matters: Prevents data corruption in sensitive control systems.
Solutions: Braided shielding (85% coverage) vs. foil shielding.
2.9 Flammability Rating (UL 94)
What It Measures: Resistance to flame propagation.
Why It Matters: Halts fire spread in high-risk environments like oil refineries.
Grades: V-0 (self-extinguishing) vs. HB (slow-burning).
2.10 Conductor Resistance
What It Measures: Electrical resistance per unit length (Ω/km).
Why It Matters: Lower resistance reduces energy loss and heat generation.
Testing: 4-wire Kelvin method for precision.
3. How to Test These Metrics
Lab Testing: Partner with certified labs (e.g., UL, TÜV) for standardized tests.
In-House Tools:
Multimeters for resistance/continuity checks.
Thermal cameras to detect hotspots.
Flex testers (e.g., DIN 72551 for bend cycles).
Documentation: Always request test reports (e.g., RoHS, REACH compliance).
4. Case Study: Avoiding Failure in Automotive Robotics
A European car manufacturer faced repeated signal losses in its welding robots. Analysis revealed undersized conductors (high resistance) and poor EMI shielding. By switching to shielded, high-flex cable harnesses with UL 94 V-0 rating:
Downtime reduced by 60%.
Energy savings: 12% due to lower conductor resistance.
5. FAQs
Q1: How often should I retest cable harnesses?
A: Annually for harsh environments; every 2–3 years for moderate use.
Q2: Can I mix different shielding types in one harness?
A: Yes (e.g., foil + braid), but ensure proper grounding to avoid noise.
Q3: What’s the cost of ignoring these metrics?
A: One automotive plant lost $500k/hour due to a single cable fire.
6. Conclusion & Resources
Selecting industrial cable harnesses isn’t just about specs—it’s about risk mitigation. Use this checklist to partner with suppliers who prioritize transparency and compliance.