What Are the Three Main Components of a Cable Assembly
- Conductor: The Pathway for Electrical Current
The conductor is the central component that carries electrical current or signals. Its material and design directly impact conductivity, flexibility, and durability.
Key Materials:
Copper: The most common choice due to its excellent conductivity (100% IACS*) and flexibility. Variants include:
Bare Copper: Cost-effective for general wiring.
Tinned Copper: Resists corrosion in humid environments.
Stranded Copper: Flexible for robotics or repetitive motion.
Aluminum: Lightweight and cheaper than copper but 61% less conductive. Used in high-voltage power lines.
Fiber Optics: Glass or plastic fibers for high-speed data transmission (e.g., telecom networks).
Applications:
Power transmission (copper/aluminum conductors).
Signal integrity in data cables (fiber optics or shielded copper).
2. Insulation: Preventing Electrical Leakage
The insulation layer surrounds the conductor, preventing short circuits and energy loss by blocking contact with other conductors or surfaces.
Common Insulation Materials:
Material Temperature Range Key Properties Typical Uses
PVC -40°C to 105°C Affordable, flexible, moderate durability Household wiring, low-voltage systems
XLPE -40°C to 150°C High heat resistance, withstands high voltage Solar farms, industrial motors
Silicone -60°C to 200°C Extreme temperature tolerance Aerospace, steel mills
PTFE (Teflon) -200°C to 260°C Chemically inert, non-flammable Chemical plants, military
Functions:
Electrical isolation.
Protection against heat, moisture, and abrasion.
3. Jacket/Sheath: External Protection
The outer jacket shields the entire assembly from environmental, mechanical, and chemical damage. It ensures longevity and safety in harsh conditions.
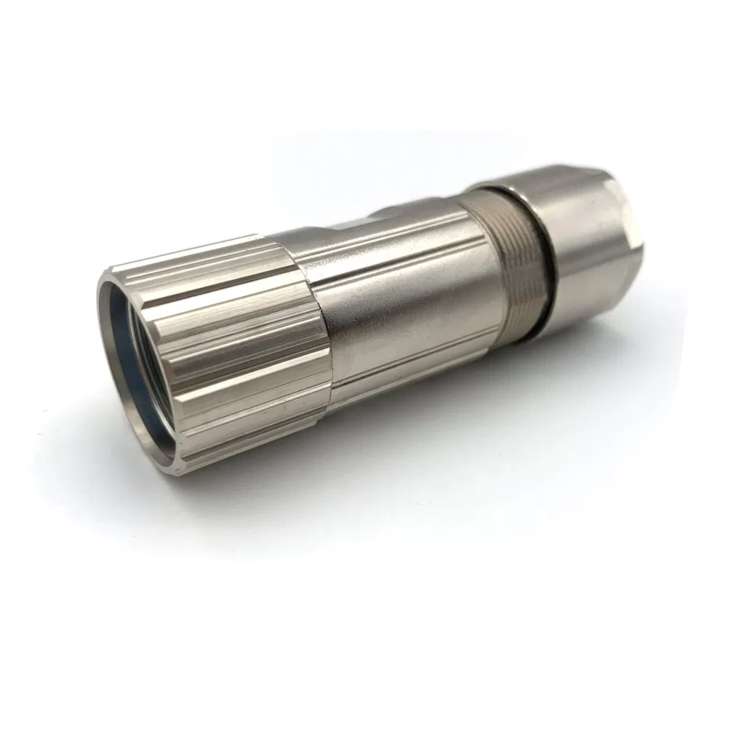
Jacket Materials and Uses:
PVC (Polyvinyl Chloride):
Pros: Low cost, flame-retardant.
Cons: Less flexible in cold temperatures.
Applications: Indoor wiring, consumer electronics.
PUR (Polyurethane):
Pros: Oil-, abrasion-, and solvent-resistant.
Applications: Industrial robots, automated machinery.
LSZH (Low Smoke Zero Halogen):
Pros: Minimal toxic fumes when burned.
Applications: Subways, ships, data centers.
Thermoplastic Elastomer (TPE):
Pros: Flexible, UV-resistant.
Applications: Outdoor solar cables, medical devices.
Additional Features:
Armoring: Steel wire or braid for crush resistance (e.g., underground cables).
EMI Shielding: Foil or braided layers to block electromagnetic interference.
How the Three Components Work Together
Conductor: Transmits energy or data.
Insulation: Keeps the current confined and safe.
Jacket: Protects against external stressors (heat, chemicals, abrasion).
Example: An automotive engine cable assembly might use:
Tinned copper conductors (for vibration resistance).
Silicone insulation (to handle under-hood heat).
PUR jacket (to resist oil and coolant exposure).
Industry Standards and Compliance
UL 62: Standards for flexible cords and cables.
IEC 60502: Specifications for power cable insulation and jackets.
RoHS: Restricts hazardous substances in materials.
Why Material Selection Matters
Temperature: Silicone or PTFE insulation/jackets for extreme heat.
Flexibility: Stranded conductors + TPE jackets for robotic arms.
Safety: LSZH jackets in public spaces to reduce fire risks.