What Materials Are Used in Industrial Cable Assemblies
- Conductors: The Core of Power and Signal Transmission
The conductor is the central element responsible for transmitting electrical power or signals. Common materials include:
Copper: The most widely used conductor due to its excellent conductivity, flexibility, and resistance to corrosion.
Aluminum: A lightweight, cost-effective alternative for high-voltage applications, though less conductive than copper.
Fiber Optics: Glass or plastic fibers for high-speed data transmission in environments prone to electromagnetic interference (EMI).
2. Insulation: Protecting Against Electrical Hazards
Insulation materials surround conductors to prevent electrical leakage and short circuits. Key types include:
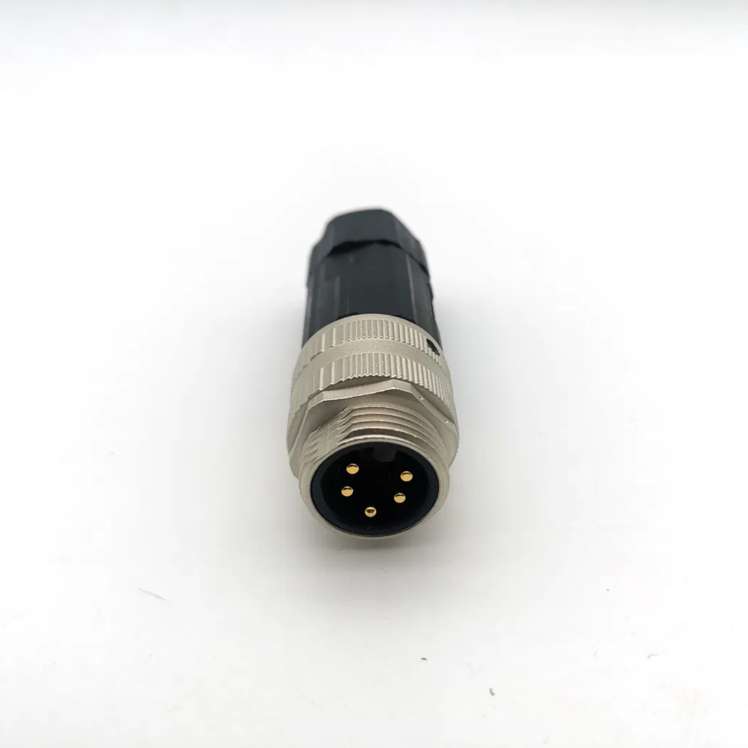
PVC (Polyvinyl Chloride): Affordable and flexible, ideal for general-purpose applications with moderate temperature ranges (-40°C to 105°C).
XLPE (Cross-Linked Polyethylene): Superior heat resistance (up to 150°C) and used in high-voltage power cables.
TPE (Thermoplastic Elastomer): Combines flexibility with resistance to oils, chemicals, and abrasion.
Silicone: Withstands extreme temperatures (-60°C to 200°C) and is common in heavy industrial or aerospace settings.
3. Sheathing/Jacketing: Shielding from External Stress
The outer jacket protects the cable from environmental and mechanical damage. Materials vary based on application needs:
PVC Jackets: Offer basic protection against moisture and abrasion.
PUR (Polyurethane): Highly resistant to oils, solvents, and repeated flexing, making it ideal for robotics and automation.
TPU (Thermoplastic Polyurethane): Balances toughness, flexibility, and resistance to UV radiation.
LSZH (Low Smoke Zero Halogen): Critical for safety in confined spaces (e.g., tunnels, submarines), as it emits minimal toxic smoke when exposed to fire.
4. Shielding: Blocking Electromagnetic Interference
Shielding materials prevent EMI from disrupting signal integrity. Two primary types are used:
Braided Shields: Woven copper or aluminum strands provide robust EMI protection and mechanical strength.
Foil Shields: Aluminum or copper foil wrapped around conductors for lightweight, cost-effective EMI shielding.
Note: Some assemblies combine both for maximum protection in high-interference environments.
5. Connectors and Terminals: Ensuring Secure Connections
Connectors are typically made from:
Metal Alloys: Brass, stainless steel, or nickel-plated contacts ensure conductivity and corrosion resistance.
High-Temperature Plastics: Materials like PEEK (Polyether Ether Ketone) or PTFE (Teflon®) are used in connectors for extreme heat or chemical exposure.
6. Fillers and Strength Members: Enhancing Durability
Fillers: Non-conductive materials like polyester yarn or aramid fibers fill gaps between components, improving structural integrity and preventing tangling.
Strength Members: Aramid fibers (e.g., Kevlar®) or steel wire are added to cables subjected to heavy pulling forces (e.g., elevators, cranes).
7. Specialized Coatings
For unique environments, additional coatings may be applied:
Anti-Corrosive Coatings: Protect against saltwater or chemical exposure in marine or chemical plants.
Flame-Retardant Additives: Meet safety standards for fire-prone areas.
Key Considerations for Material Selection
Choosing the right materials depends on factors such as:
Environmental Conditions: Temperature extremes, moisture, UV exposure, or chemical contact.
Mechanical Stress: Vibration, flexing, or tensile loads.
Regulatory Compliance: Certifications like UL, RoHS, or MIL-SPEC may dictate material choices