Which Materials Are Suitable for Cable Assemblies in High-Temperature...
Meta Description: Discover the best materials for cable assemblies in high-temperature environments. Learn about heat-resistant polymers, insulation options, and practical tips for durability and safety.
High-temperature environments, such as industrial manufacturing, automotive engine compartments, aerospace systems, and energy production facilities, demand cable assemblies that can withstand extreme heat without degrading. Selecting the right materials is critical to ensure safety, performance, and longevity. In this guide, we’ll explore the most suitable materials for high-temperature cable assemblies, their properties, and practical considerations for your applications.
Understanding the Challenges of High-Temperature Environments
Cables exposed to high temperatures face multiple risks:
- Insulation breakdown: Heat can melt or crack insulation, leading to short circuits.
- Conductor oxidation: Prolonged heat exposure weakens conductive metals.
- Loss of flexibility: Materials may become brittle, increasing the risk of damage.
- Chemical degradation: Heat accelerates reactions with oils, solvents, or moisture.
To combat these issues, materials must offer thermal stability, chemical resistance, and mechanical strength.
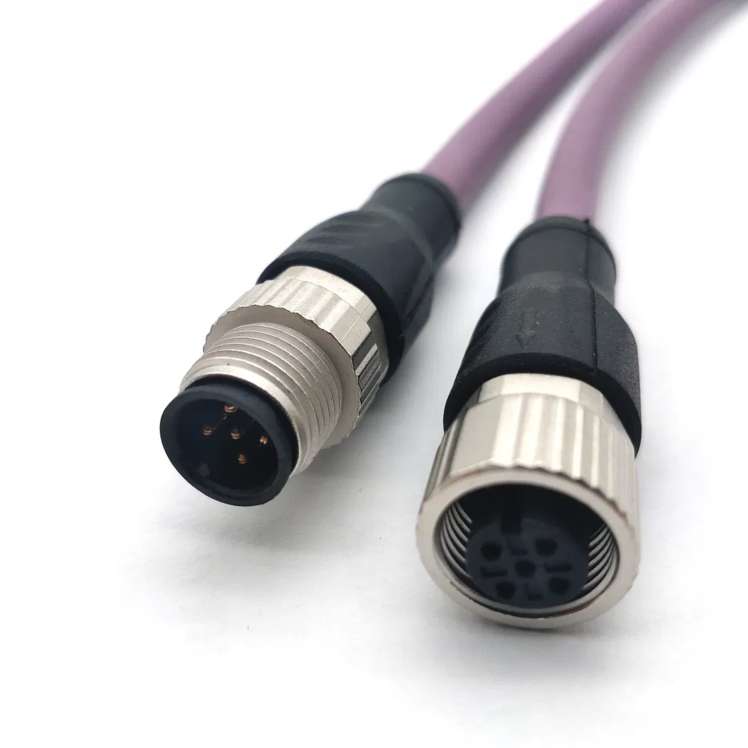
Key Materials for High-Temperature Cable Assemblies
1. High-Temperature Insulation Materials
a. Silicone Rubber
- Temperature Range: -60°C to +200°C (short-term up to 250°C).
- Benefits: Flexible, flame-retardant, and resistant to moisture and UV radiation.
- Applications: Automotive wiring, industrial heaters, and LED lighting systems.
b. PTFE (Polytetrafluoroethylene)
- Temperature Range: -200°C to +260°C.
- Benefits: Excellent chemical resistance, low friction, and non-flammability.
- Drawbacks: Higher cost and less flexibility compared to silicone.
- Applications: Aerospace, chemical processing, and medical equipment.
c. FEP (Fluorinated Ethylene Propylene)
- Temperature Range: -200°C to +200°C.
- Benefits: Similar to PTFE but easier to process; retains flexibility at high temps.
- Applications: Data cables, food processing machinery.
d. Polyimide (Kapton)
- Temperature Range: -269°C to +400°C.
- Benefits: Thin, lightweight, and resistant to radiation.
- Applications: Spacecraft, military electronics, and downhole drilling tools.
2. Heat-Resistant Conductor Materials
a. Nickel-Plated Copper
- Temperature Tolerance: Up to 450°C.
- Benefits: Oxidation resistance and high conductivity.
- Use Cases: Power transmission in foundries or glass manufacturing.
b. Stainless Steel
- Temperature Tolerance: Up to 800°C.
- Benefits: Extreme heat resistance but lower conductivity.
- Applications: Furnace wiring, nuclear reactors.
c. Silver-Plated Copper
- Temperature Tolerance: Up to 200°C.
- Benefits: Enhanced conductivity and corrosion resistance.
- Applications: Aerospace and defense systems.
3. Protective Jacketing Materials
a. Fiberglass
- Temperature Range: Up to 500°C.
- Benefits: Non-flammable and chemically inert.
- Applications: Welding cables, kiln wiring.
b. Ceramic Fiber
- Temperature Range: Up to 1,200°C.
- Benefits: Exceptional thermal insulation for extreme conditions.
- Applications: Steel mills, power generation turbines.
c. Metal Braids (Aluminum or Steel)
- Benefits: Mechanical protection and heat dissipation.
- Applications: Automotive exhaust sensors, industrial robotics.
Practical Tips for Selecting Materials
- Match Temperature Ratings to Operating Conditions: Ensure materials exceed the maximum expected temperature.
- Consider Chemical Exposure: Choose materials resistant to oils, acids, or solvents in your environment.
- Prioritize Flexibility: In dynamic applications (e.g., robotics), use silicone or FEP to prevent cracking.
- Check Compliance Standards: Look for UL, MIL-SPEC, or RoHS certifications for safety and quality.
- Factor in Cost vs. Lifespan: High-performance materials like PTFE may have higher upfront costs but lower long-term maintenance.
Case Study: Cable Assemblies in Oil & Gas Drilling
In oil drilling, cables face temperatures exceeding 150°C, high pressure, and corrosive fluids. A combination of PTFE insulation, nickel-plated copper conductors, and stainless steel braiding ensures reliability. This setup prevents insulation meltdown and conductor oxidation, reducing downtime and repair costs.
Maintenance and Installation Best Practices
- Avoid Tight Bends: High-temperature materials can become brittle; use gradual bends.
- Use Heat-Resistant Connectors: Pair cables with connectors rated for similar temperatures.
- Regular Inspections: Check for cracks, discoloration, or stiffness, which signal material degradation.