Which Oil and Gas Projects Use High-Voltage Cables
High-voltage (HV) cables play a pivotal role in the oil and gas industry, enabling the safe and efficient transmission of power across vast, remote, and challenging environments. From offshore drilling platforms to onshore processing facilities, HV cables (typically rated at 1 kV and above) are deployed in projects that demand reliable energy distribution, resistance to extreme conditions, and compliance with stringent safety standards.
1. Offshore Drilling Platforms
Offshore oil and gas operations require robust power infrastructure to support drilling, pumping, and safety systems. HV cables are critical for:
Subsea Power Distribution:
Projects like Norway’s Ekofisk Field and Brazil’s Pre-Salt Fields use HV submarine cables (33–132 kV) to supply electricity to subsea pumps, Christmas trees (wellheads), and remote-operated vehicles (ROVs).
Cables are armored with steel wire and insulated with cross-linked polyethylene (XLPE) to withstand high pressure and corrosive seawater.
Platform Electrification:
The Johan Sverdrup Field in the North Sea employs HV cables (22 kV) to power drilling rigs, gas compression systems, and living quarters on platforms.
2. Onshore Processing Facilities
Large-scale onshore facilities, such as refineries and gas processing plants, depend on HV cables for high-power equipment:
Gas Compression Stations:
The Trans-Anatolian Natural Gas Pipeline (TANAP) in Turkey uses 66 kV cables to power compressors that maintain gas flow over 1,850 km.
HV cables here feature ethylene propylene rubber (EPR) insulation for thermal stability in desert climates.
LNG Liquefaction Plants:
Australia’s Gorgon LNG Project relies on 110 kV cables to drive massive refrigeration units that cool natural gas to -162°C.
Cables are designed with fire-resistant LSZH (low-smoke zero-halogen) jackets to mitigate fire risks in hazardous areas.
3. Pipeline Heating and Monitoring
HV cables are integrated into pipelines to prevent blockages and ensure operational integrity:
Electrically Heat-Traced Flowlines (EHTF):
In Canada’s Alberta Oil Sands, buried HV cables (6–25 kV) provide heat to viscous bitumen pipelines, reducing viscosity and enabling flow in freezing temperatures.
These cables use mineral-insulated (MI) designs with copper sheathing for durability.
Pipeline Cathodic Protection:
The Keystone Pipeline in the U.S. employs HV DC systems (1–5 kV) to deliver current for corrosion prevention across thousands of kilometers.
4. Floating Production Storage and Offloading (FPSO) Vessels
FPSOs, which process and store oil at sea, require compact yet powerful HV systems:
Power Generation and Distribution:
The Ichthys FPSO off Australia’s coast uses 11 kV cables to connect gas turbines to processing modules and thrusters.
Cables are oil-resistant and rated for continuous operation in high-humidity marine environments.
Dynamic Cables for Mooring Systems:
Brazil’s Lula Field FPSOs utilize HV dynamic cables (33 kV) with flexible EPDM insulation to accommodate vessel movement and wave stresses.
5. Subsea Production Systems
Deepwater projects leverage HV cables to power subsea equipment:
All-Electric Subsea Controls:
The Åsgard Field in Norway uses 3.6 kV cables to operate subsea valves, sensors, and control systems, replacing traditional hydraulic systems with electric actuators.
These cables integrate fiber optics for real-time data transmission alongside power delivery.
Multiphase Pumping:
The Troll Oil Field employs HV cables (72 kV) to drive subsea pumps that enhance oil recovery from low-pressure reservoirs.
6. Renewable-Integrated Oil and Gas Projects
As the industry shifts toward decarbonization, HV cables bridge fossil fuel and renewable energy systems:
Hybrid Power Systems:
The Hywind Tampen Project (Norway) powers offshore oil platforms with floating wind turbines connected via 66 kV submarine cables.
Cables are designed for dynamic seabed conditions and high mechanical stress.
Carbon Capture and Storage (CCS):
HV cables (10–30 kV) support CCS projects like Chevron’s Gorgon CO2 Injection Facility, powering compressors that sequester CO2 underground.
Technical Requirements for HV Cables in Oil and Gas
Cables in these projects must meet rigorous criteria:
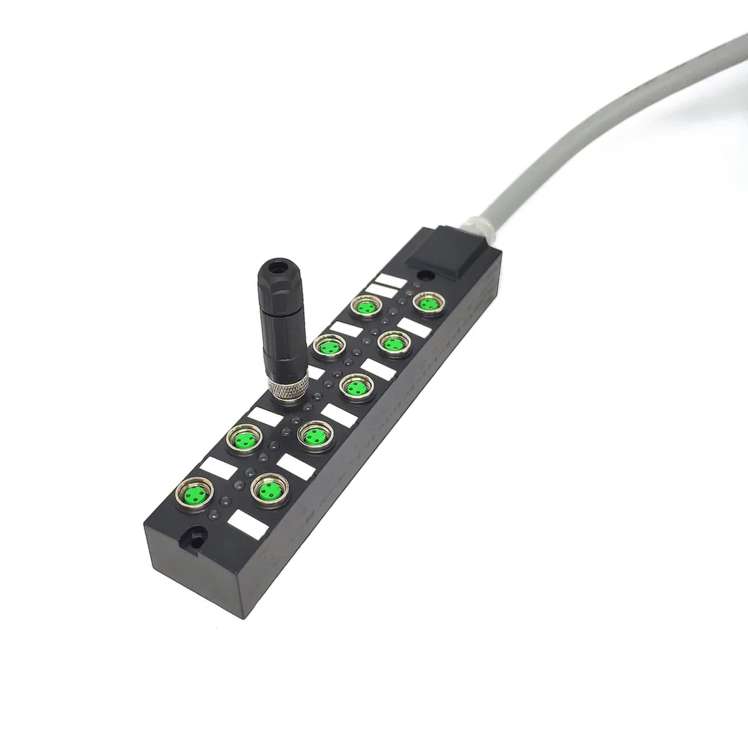
Environmental Resistance:
Materials like HDPE (high-density polyethylene) or ETFE (ethylene tetrafluoroethylene) for chemical, UV, and abrasion resistance.
Fire and Explosion Safety:
Compliance with IEC 60092 (marine cables) and API 14F (offshore electrical systems).
Long-Distance Reliability:
HVDC (high-voltage direct current) systems minimize losses in subsea transmission over hundreds of kilometers.